How to achieve operational agility without disrupting product quality and plant productivity
Posted: March 24, 2022
Our latest white paper, “Agility for competitiveness: Transforming manufacturing operations for business agility,” compiles the latest research on the changing consumer products industry. It offers industry-tailored digital transformation solutions.
When the pandemic began, many manufacturers found that their operations, optimized for overall equipment efficiency, were not well-equipped to respond to volatile market demands—and their ripple effects throughout the global supply chain. The pandemic saw a surge in e-commerce, which grew two to five times faster than before the pandemic, and the shift away from brick-and-mortar retail stores is expected to be the new normal. For manufacturers, these new channels to market mean shrinking lead times, decreasing lot sizes, and faster production cycles. Consumers now expect convenient purchasing and prompt delivery, and they also expect full transparency into delivery times and the product origin. At the same time, the pandemic hastened some existing challenges, like a retiring workforce and increased employee turnover, and introduced a new one—the difficulty of attracting talent. Forthcoming sustainability mandates are pushing energy, emission, and waste reduction requirements that will bring further changes to operations and will call for greater documentation for compliance.
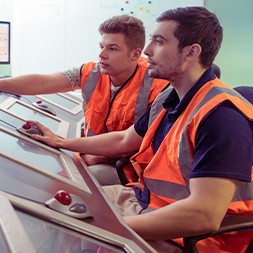
According to a 2021 report conducted by the World Economic Forum, 56% of the 3,000 CEOs surveyed listed agility and flexibility as their top strategic priorities to meet the challenges in the manufacturing landscape.
Transforming manufacturing operations for business agility
While overall equipment efficiency was a sufficient paradigm in the pre-pandemic manufacturing landscape, today’s landscape requires leveraging digital technologies to optimize the supply chain for responsiveness and manufacturing plants for efficiency and adaptability to a more dynamic environment. Advanced digital production planning, scheduling, and execution capabilities allow manufacturers to align operational planning with the realities of the plant floor for efficient and compliant schedule execution to deliver business-critical orders, on time and in full, at the lowest possible cost. Providing real-time visibility into plant resources and capacity ensures that operational plans are feasible, so manufacturers can accurately plan for meeting demand, even when demand fluctuates.
Multi-site digital transformation
The distributed plant networks of manufacturing enterprises require a multi-site digital transformation strategy that helps companies synergize across plants. Digital twin technology can facilitate standardization of processes, metrics, and reporting for a quick roll-out across multiple sites. The digital twin enables manufacturers to abstract the manufacturing plant through an agnostic industrial operations platform and modern manufacturing execution application. By enabling complete visibility into plant operations, resources, and assets, a digital twin offers a much-needed dimension of what the plant network is capable of delivering. The digital twin gives manufacturers the ability to run “what if” scenarios, so manufacturers can determine the best outcomes virtually. Abstracting multiple sites in a digital twin arms manufacturers with the ability to transform operations across multiple sites, though the sites may have differing setups and practices.
Related blog posts
Stay in the know: Keep up to date on the latest happenings around the industry.