Was ist ein digitaler Zwilling?
Ein digitaler Zwilling ist eine virtuelle Darstellung eines physischen Objekts, Prozesses oder Systems. Es ist eine digitale Nachbildung, die das Verhalten, die Eigenschaften und die Leistung seines realen Gegenstücks in Echtzeit simuliert.
Grundsätzlich beinhaltet ein digitaler Zwilling Daten, Modelle und Analysen in unterschiedlichen Anteilen und eine Visualisierungserfahrung. Ein digitaler Zwilling kombiniert alle möglichen Datensätze aus Engineering und Betrieb und erweitert sie um eine oder mehreren Arten von First-Principle-Modellen und künstlicher Intelligenz.
Sobald die Daten aggregiert sind, können Benutzer im gesamten Unternehmen die Daten in einem zweckmäßigen Format visualisieren, um bestimmte Anwendungsfälle zu meistern. Ein digitaler Zwilling kann den Entwurf und den Bau eines Großprojekts oder den täglichen Betrieb einer Industrieanlage oder eines Prozesses modellieren.
Hier sind die wichtigsten Komponenten im Detail:
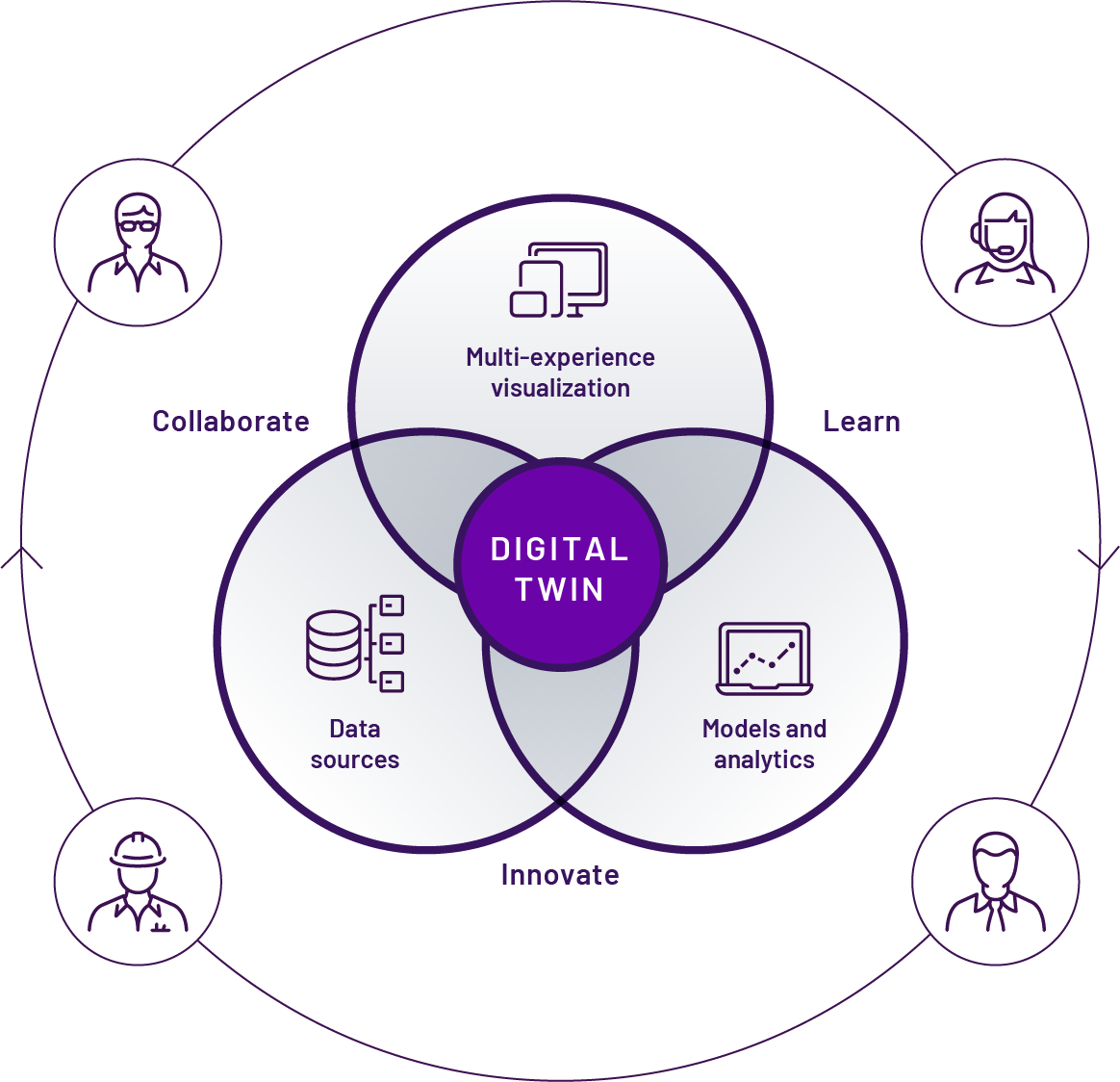
- Gesammelte und aggregierte Daten mit Kontext: Digitale Zwillinge stützen sich auf einen kontinuierlichen Strom von Daten und Informationen aus mehreren Quellen wie Sensoren, Anlagen, Systemen und Geräten, um den Status und Zustand des physischen Objekts oder Prozesses in Echtzeit zu erfassen.
- Analytische Fähigkeiten: Digitale Zwillinge nutzen KI-/Modelle des maschinellen Lernens, um die gesammelten Daten zu analysieren und Einblicke in das Verhalten, die Leistung und potenzielle Probleme des physischen Objekts oder Systems zu bereitzustellen.
- Integration und Modellierung von Daten: Die gesammelten Daten werden verarbeitet, integriert und in ein dynamisches Modell umgewandelt, das die physische Anlage oder den Prozess genau darstellt.
- Visualisierungsebene für mehrere Erlebnisse: Die rollenbasierte Visualisierung ermöglicht dem Benutzer den Zugriff auf Daten, die in einer für einen bestimmten Zweck geeigneten Form dargestellt werden. Der Benutzer in der Werkstatt sieht die für seine KPI relevanten Informationen, während die Führungsebene dieselben Daten in einem für das gesamte Management relevanteren Kontext betrachtet.
Digitale Zwillinge bei AVEVA
Bei AVEVA bieten wir unseren Kunden „einen intelligenten Zwilling“ während des gesamten industriellen Lebenszyklus. Unsere industrielle Plattform CONNECT bildet zusammen mit unseren KI-Anwendungen und Visualisierungslösungen die Grundlage für einen digitalen Zwilling. Mit „einem intelligenten Zwilling“ meinen wir einen digitalen Zwilling, der mit Ihrem konzeptionellen Entwurf beginnen und mit Ihrem Projekt bis hin zu Betrieb und zur Optimierung reifen kann.
Unsere Software verbindet technische Daten mit Betriebsdaten und leitet sie dann zu unserer industriellen Plattform weiter, wo sie konsolidiert, bereinigt und aggregiert werden, um eine Darstellung von Geräten, Systemen oder Anlagen zu erstellen.
Da sich unsere Plattform nahtlos in IoT-Geräte, KI-Algorithmen und Datenanalysetools integrieren lässt – ob es sich um Tools von AVEVA oder Tools von Drittanbietern handelt – können Unternehmen ihre vorhandenen Investitionen nutzen.
Organisationen, mit denen wir zusammenarbeiten, können digitale Zwillinge für Anwendungsfälle im gesamten industriellen Lebenszyklus verwenden, von der Entwurfs- und Bauphase bis hin zu Betrieb und Optimierung. Organisationen profitieren von kombinierten Daten- und Informationsquellen und verbessern so die Entscheidungsfindung und Zusammenarbeit zwischen Teams. Das kann beispielsweise eine Verbesserung der Effizienz durch die Vermeidung ungeplanter Ausfallzeiten oder Störungen in der Wertschöpfungskette sein.
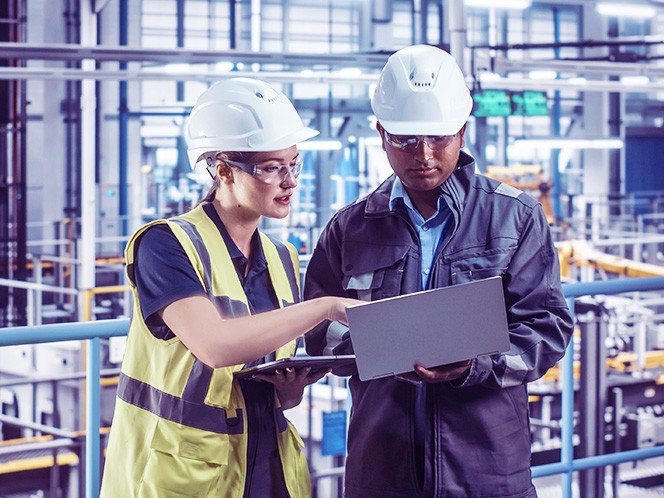
Wie funktioniert ein digitaler Zwilling?
In der Welt der industriellen Organisationen ist ein digitaler Zwilling ein leistungsstarkes Tool, das eine zentrale Sicht auf die gesamte Organisation bietet. Doch wie funktioniert ein digitaler Zwilling genau? Datenmanagement und Infrastruktur ebenso wie die Erfassung, Konsolidierung und Aggregation dieser Daten spielen eine entscheidende Rolle für das Funktionieren eines digitalen Zwillings. Durch das Sammeln von Daten aus verschiedenen Quellen wie:
- Lebendige Daten aus den Überwachungs- und Steuerungsaspekten von Automatisierungssystemen;
- Rohdaten – einschließlich Technik und Betrieb, Echtzeit und historisch – von Prozessanlagen, Versorgungssystemen und anderen externen Quellen:
- Relevante Daten zum Gerätedesign, Marktpreise, Umgebungsbedingungen, Geschäftsindikatoren und Daten zum Verbraucherverhalten;
Alle Daten, die sich auf das Geschäft beziehen, können Teil des digitalen Zwillings sein. Diese kontextualisierten 1D-, 2D-, 3D- und operativen Daten werden dann durch First-Principle-Modellierung oder/und Analytik und KI erweitert, um tiefere Einblicke in die Herausforderung zu erhalten, die das Unternehmen zu bewältigen versucht. Analytik und KI bilden „das Gehirn“ des digitalen Zwillings. Die Analyseebene ermöglicht es dem digitalen Zwilling, über eine statische Echtzeitdarstellung der Anlage oder des Prozesses hinauszugehen und zu prognostizieren, wie sich die Anlage oder der Prozess unter Berücksichtigung einer Reihe von Variablen in Zukunft verhalten wird.
Echtzeitsynchronisierung und Simulation sind wesentliche Merkmale eines digitalen Zwillings. Wenn sich die physische Anlage oder der Prozess ändert, aktualisiert sich der digitale Zwilling selbst in Echtzeit. Diese Synchronisierung stellt sicher, dass die virtuelle Darstellung korrekt und aktuell bleibt.
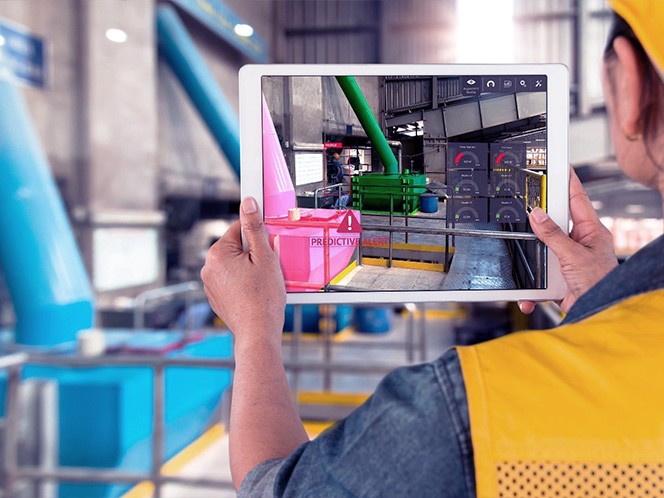
Durch die Simulation verschiedener Szenarien und prädiktive Algorithmen können Unternehmen ihre Betriebsabläufe testen und optimieren, ohne Risiken für die physischen Anlagen oder Prozesse einzugehen. Diese Fähigkeit ermöglicht eine proaktive Entscheidungsfindung und die Identifizierung potenzieller Probleme, bevor sie auftreten.
Mit einer fortschrittlichen Visualisierung können Unternehmen einen ganzheitlichen Überblick über ihre Anlagen oder Prozesse in einer virtuellen Umgebung erhalten.
Diese visuelle Darstellung ermöglicht es den Stakeholdern, die Leistung in Echtzeit zu überwachen, Muster zu erkennen und Daten effektiv zu analysieren. Darüber hinaus bieten in den digitalen Zwilling integrierte Analysetools präskriptive Analysen mit verwertbaren Erkenntnissen, anhand derer Unternehmen datengestützte Entscheidungen treffen und rechtzeitig Maßnahmen ergreifen können, um kontinuierliche Verbesserungen voranzubringen.
Digitale Zwillinge über den gesamten industriellen Lebenszyklus
Die Nutzung des digitalen Zwillings unterscheidet sich von Branche zu Branche und von Unternehmen zu Unternehmen – und jede Organisation hat ihre eigenen Argumente, warum sie ihn verwenden. Ein digitaler Zwilling ist am besten anhand der praktischen Möglichkeiten definiert, mit denen er Daten nutzen kann, um Erkenntnisse zu liefern, die Design, Betrieb und Optimierung einer industriellen Anlage oder eines Prozesses während des gesamten Lebenszyklus unterstützen.
Hier sind vier allgemeine Bereiche, in denen die Technologie des digitalen Zwillings Positives bewirken kann:
Design und Bau. Die Einführung eines datenzentrierten Ansatzes verbessert die Transparenz und Kontrolle von der Investitionsphase bis zur Inbetriebnahme der Anlage. EPCs können weniger Zeit für die Überarbeitung des Designs aufwenden und die Lieferung erfolgt mit größerer Wahrscheinlichkeit termingerecht und innerhalb des Budgets.
Betrieb. Durch den Zugriff auf Echtzeit- und historische Daten kann der Anlagenbetreiber das tatsächliche Verhalten vergleichen, modellieren und daraus Erkenntnisse gewinnen. Die Ergebnisse können der Belegschaft mehr Handlungsfreiheit geben, die Produktivität verbessern, unnötige Arbeiten reduzieren und die Zuverlässigkeit verbessern, unter gleichzeitiger Beibehaltung von Sicherheit und Nachhaltigkeit.
Optimierung. KI/maschinelles Lernen und First-Principles-Modelle liefern Erkenntnisse und Anleitungen für den Anlagenbetrieb. Mit nützlichen Benchmarks, auf die sie sich beziehen, können Betreiber fundiertere Entscheidungen treffen, ein Gleichgewicht zwischen Leistung und Zuverlässigkeit mit Kosteneffizienz herstellen und die Rentabilität steigern.
Nachhaltigkeit. Nachverfolgung der Fortschritte in Echtzeit gegenüber Nachhaltigkeit-KPI und -Ziele im gesamten Unternehmen kann dazu beitragen, Abfall zu minimieren, die Zufriedenheit der Belegschaft zu erhöhen, Umweltschutzvorschriften einzuhalten und die soziale Verantwortung des Unternehmens zu stärken.
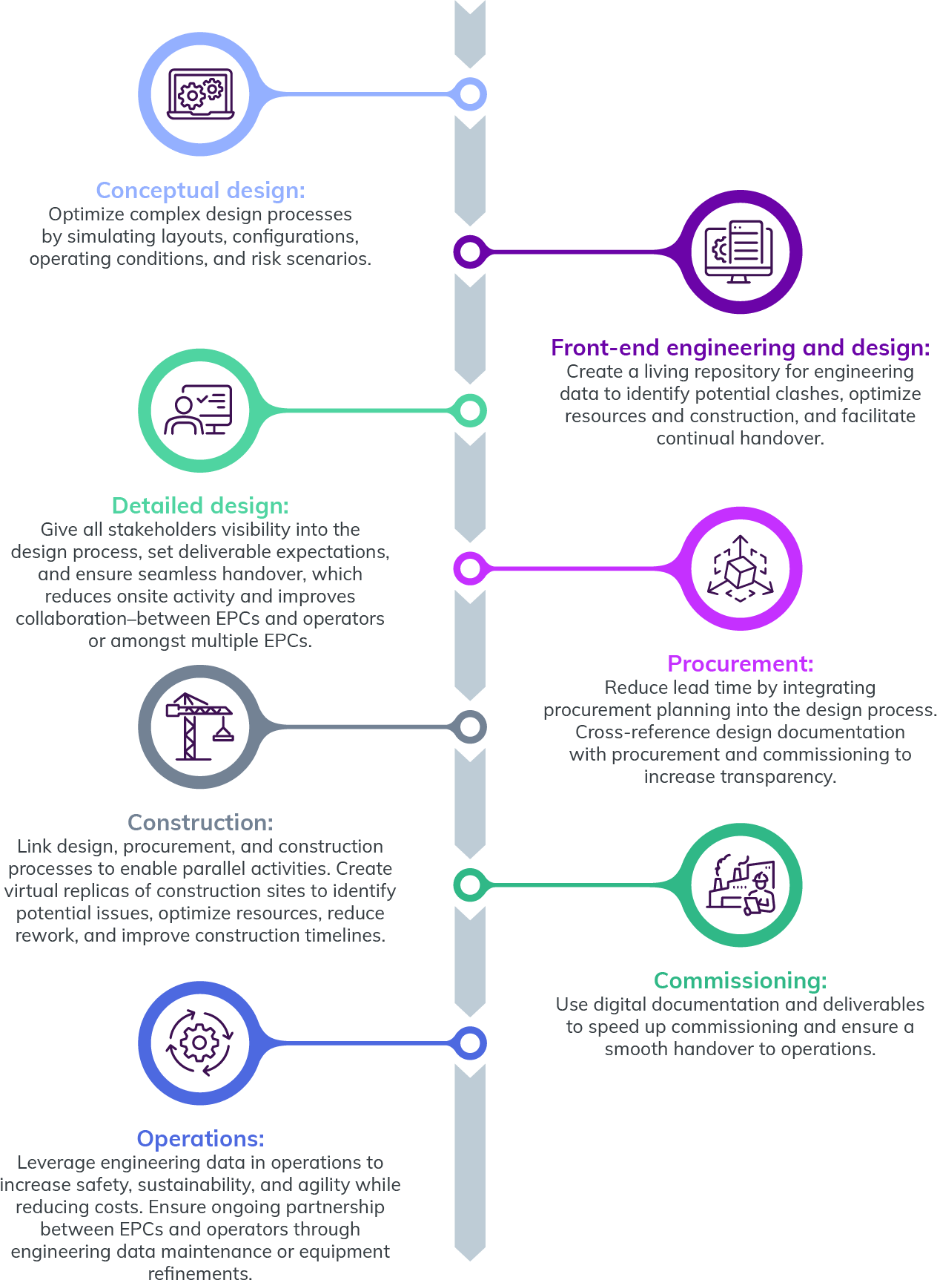
Der digitale Zwilling umfasst den gesamten Lebenszyklus eines Projekts vom Entwurf bis zur Außerbetriebnahme.
Vorteile digitaler Zwillinge
Digitale Zwillinge haben das Potenzial, Unternehmen zu revolutionieren und sind im heutigen Wettbewerbsumfeld die Voraussetzung für Wachstum. Durch die Nutzung dieser Technologie können Organisationen neue Möglichkeiten erschließen und ein noch nie dagewesenes Maß an Effizienz erreichen.
Hier sind die wichtigsten Vorteile für Industrieunternehmen:
Verbesserte Entscheidungsfindung- und Prognosefähigkeiten: Durch die Erstellung einer virtuellen Nachbildung von physischen Anlagen oder Prozessen können Unternehmen Daten überwachen und analysieren, um Trends, Muster und Anomalien zu erkennen. Digitale Zwillinge erleichtern die Zusammenarbeit und Kommunikation zwischen verschiedenen Stakeholdern wie Ingenieuren, Betreibern und Managern. Dies ermöglicht eine proaktive Entscheidungsfindung ebenso wie die Fähigkeit, potenzielle Probleme vorherzusehen und zu verhindern, bevor sie auftreten. Da sie korrekte und aktuelle Informationen zur Hand haben, können Entscheidungsträger ihre Abläufe optimieren und bessere Ergebnisse erzielen.
Optimierte Leistung und Effizienz: Durch die Simulation und das Testen unterschiedlicher Szenarien können Unternehmen Bereiche mit Verbesserungspotenzial identifizieren und gezielte Strategien implementieren. In der Fertigung können digitale Zwillinge beispielsweise dazu beitragen, Produktionsprozesse zu optimieren, Abfall zu reduzieren und die Produktqualität zu verbessern. Durch die Nutzung von Echtzeitdaten und fortschrittlichen Analysen können Organisationen Engpässe aufdecken, Abläufe rationalisieren und die Ressourcennutzung maximieren. Das Ergebnis sind eine verbesserte Produktivität, geringere Kosten und eine gesteigerte Wettbewerbsfähigkeit.
Reduzierte Ausfallzeiten und Wartungskosten: Einer der wichtigsten Vorteile digitaler Zwillinge ist die Fähigkeit, Ausfallzeiten und Wartungskosten zu minimieren. Durch die Überwachung ihrer Anlagen in Echtzeit können Organisationen potenzielle Probleme frühzeitig erkennen und vorbeugende Wartungsarbeiten planen. Dieser proaktive Ansatz trägt dazu bei, unerwartete Ausfälle zu verhindern, ungeplante Ausfallzeiten zu reduzieren und die Lebensdauer von Anlagen zu verlängern. Durch die frühzeitige Identifizierung des Wartungsbedarfs können Unternehmen ihre Wartungspläne optimieren, Unterbrechungen minimieren und die Gesamtwartungskosten senken.
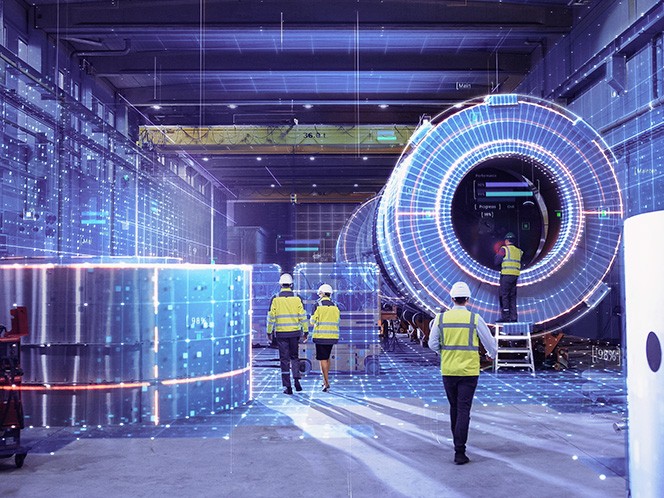
Erfolgsberichte der Kunden
Das Zentrum für Echtzeit-Datenvisualisierung von ADNOC ermöglicht Agilität
Die Abu Dhabi National Oil Company (ADNOC) gewinnt Sichtbarkeit in alle Betriebsabläufe und verbessert seine geschäftliche Agilität durch die Integration und Überwachung von über 10 Millionen Tags in 120 Dashboards.
SCG Chemicals erstellt einen operativen digitalen Zwilling
SCG Chemicals nutzt seine virtuelle Anlage, um den Betrieb mit Dashboards für Gerätestatus, Alarme und Leistung zu optimieren.
bp verbessert Zusammenarbeit und Sicherheit mit ACE Digital Twin
Mit einem digitalen Zwilling der Produktionsanlage in Azeri Central East können die Teams von bp aus der Ferne zusammenarbeiten, um einen sicheren und zuverlässigen Betrieb sicherzustellen.
PETRONAS spart Millionen durch frühzeitige Fehlererkennung
Durch die Vermeidung von Geräteausfällen mithilfe der KI-gestützten AVEVA Predictive Analytics in der Cloud spart PETRONAS 33 Mio. USD.
Ausgewählte Digital-Twin-Produkte
AVEVA Asset Information Management
AVEVA Asset Information Management ist eine leistungsstarke webbasierte Informationsmanagement-Lösung für das Engineering und die Betriebsführung. Sie führt Informationen aus verschiedenen Quellen und in verschiedenen Formaten zusammen. So können Benutzer in ihrem Unternehmen sicher auf die Daten digitaler Assets zugreifen, sie visualisieren, validieren und gemeinsam bearbeiten.
AVEVA Predictive Analytics
Früher bekannt als PRiSM Predictive Asset Analytics
Ein einheitliches, mehrdimensionales Informationsmodell aggregiert Daten aus verschiedenen Quellen und bietet Kontextinformationen für Reporting- und Dashboard-Tools. Verbessern Sie die Anlagenleistung nahezu in Echtzeit, indem Sie in Ihrer Business Intelligence Software umfangreiche Analysen Ihrer Industriedaten ermöglichen.
AVEVA Process Simulation – Entwickeln Sie nachhaltige Prozesse in den Bereichen Chemie und Energie mit einer innovativen, integrierten Plattform
Zuvor bekannt als SimCentral Simulation Platform
Schaffen Sie nachhaltige Prozesse, Produkte und Anlagen in einer vom Markt vorgegebenen Geschwindigkeit. AVEVA Process Simulation geht über lineare, verschwenderische Arbeitsabläufe hinaus und ermöglicht eine zirkuläre, nachhaltige Welt.
AVEVA E3D Design
Früher bekannt als AVEVA Everything 3D
Die fortschrittlichste und leistungsstärkste Lösung für das 3D-Design, die multidisziplinäres Design ermöglicht, um die Effizienz in Konstruktion und Design zu maximieren.
CONNECT
Unsere Industrial-Intelligence-Plattform: Sicherer Zugriff auf das umfassendste und vollständigste Software-as-a-Service-Portfolio (SaaS) für die Industrie, optimiert mithilfe von leistungsstarker künstlicher Intelligenz (KI) für die Industrie.