Autonomous operations in refineries
Posted: June 14, 2024
As with confusion about “digital twin”, “asset performance management” and other new technology initiatives, “autonomous operations” might seem vague and like a fantasy for many refineries. It’s like the old joke about advanced process control: “What is advanced process control? Something more advanced than what we have now.”
Autonomous operations are simply a set of functions that maximize safety, yield and mechanical integrity by increasing the sensing, automation, prescription and forecasting for operations, inspection and maintenance procedures. It addresses the following challenges:
- Increased focus on minimizing releases and in some cases, fires–large flares and fires from corrosion breakout combined with an ignition source.
- Increased focus on accelerating skills and improving work-life balance, especially for the current shrinking pool of experts.
- Increased focus on performance–higher availability, higher efficiency, lower emissions and in some cases, higher value chain agility.
Applying autonomous operations is simple pragmatism
Autonomous operations aren’t a science fiction fantasy. They are, rather, part of a pragmatic journey which correctly improves the sensing, automation, prescription and forecasting with a corresponding culture change, boosting transparency and proactivity. The following diagram summarizes one approach to applying autonomous operations, by using “centers of excellence”, typically located in cities which attract and retain new talent:
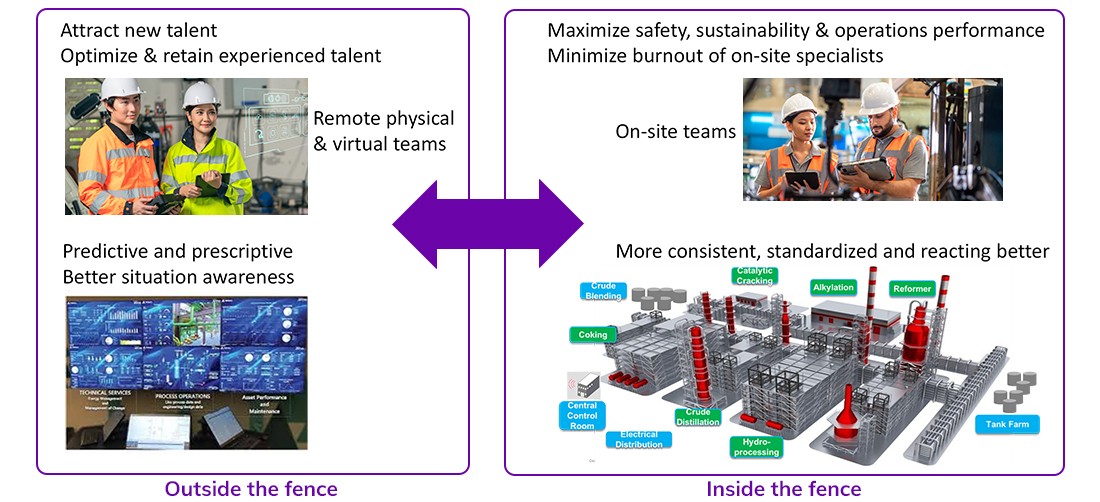
This process is much more than enhanced “monitoring”; it combines immersive training, what-if analyses performed ten times more frequently, and earlier, faster, and more frequent recommendations and actions. The diagram below shows 22 questions that require an ongoing conversation to answer, in contrast to the two traditional questions, which require only a single response, and are highlighted in red:
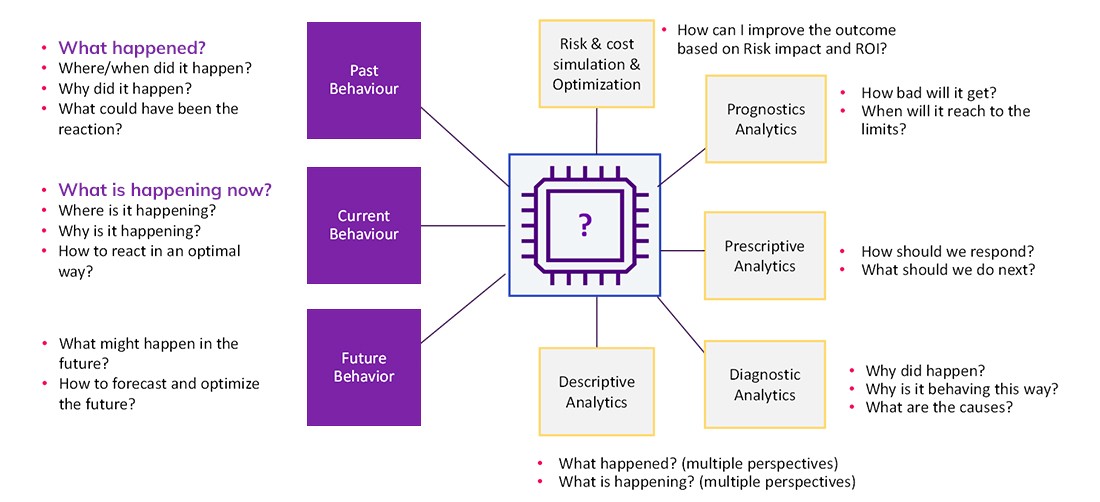
This may appear to be too visionary, too ambitious, and too fragile for many organizations; but you can implement and maintain them as a service, where the foundation is trustworthy engineering and information management. Users can then interact with a unified experience and avoid having to re-navigate across many software applications when they shift their focus from one asset to another.
You can apply this approach to varying extents, depending upon incremental value and feasibility. Process units with reactors benefit from proactive virtual centers of excellence to make better use of often-overworked experts as well as to accelerate the skills of the new talent. However, simple implementation doesn’t mean that these units will ever operate “lights out”—though light-ends units and most of utilities can. This approach isn’t new; organizations have been applying some of these elements since the 1990s. Today, refinery fleets in Asia, North America, the Middle East and Europe have applied predictive analytics for rotating and stationary equipment—and some have applied continuous forecasting of emissions and flaring. Furthermore, throughout the world, teams are constantly using more sensing and procedure automation as well as prescriptive and proactive preparation for field work—from operations through maintenance and inspection.
Using the maturity model to evaluate autonomous operations
We recommend that management overseeing this function use a “maturity model” that standardizes the description of current and target approaches. It offers a benchmark for evaluation rather than a plan for implementation. In the following diagram, you’ll see that the lowest level is ultimately acceptable if the performance is acceptable. Meanwhile, the highest level isn’t necessary for all process areas or process units.
Many refinery areas or process units are at level 2, and, for them, the realistic target is to transform to level 3. It’s important to bear in mind that one of the strategies to optimize worker productivity and improve work-life balance is to minimize the time required for less critical areas; this is the motivation to transform these areas to level 4.
The autonomous operations approach is only part of a holistic solution for any refinery, and, to be clear, the automation and safety systems aren’t the center of such an approach.
To achieve autonomous operations, you have to adapt refinery areas to enable it. In many cases, you’ll need more sensing and remote actuation as well as to modify the processes to better withstand upsets, such as flare recovery, “pacing” between process units etc. You’ll also have to adapt these areas or units for delayed maintenance and on-site inspections. Workers (employees and contractors) will need to wear “lone worker” devices to sense health, location and proximity (and this information must be governed by local worker council or union agreements).
Similarly, to achieve autonomous operations, you’ll need to focus your culture. The approach does act as a catalyst for culture change, especially because of the increased transparency. But you’ll also have to think about how both “virtual” teams (teams working together from many locations) and “co-located” teams (teams working on one floor with adjacent rooms) must have solutions designed for human factors, which reduce fatigue and stress, and make the jobs as attractive as possible, especially for the newest talent.
Training is significantly different, which transitions from procedure training to immersive experiences like video games. Many refineries and other industrial operations have consistently demonstrated skill acceleration, which helps to offset the “churn” of new talent changing jobs frequently.
So, what are the expected results for autonomous operations?
A quick summary:
- Almost no major flares
- Move up 1 Solomon quartile or stay in a high quartile.
- Energy efficiency of at least 11 %
- Reliably process lower-cost crudes to increase margins by more than USD$1.50/barrel.
Related blog posts
Stay in the know: Keep up to date on the latest happenings around the industry.