How process simulation software will help build a new green ammonia economy
Posted: October 1, 2024
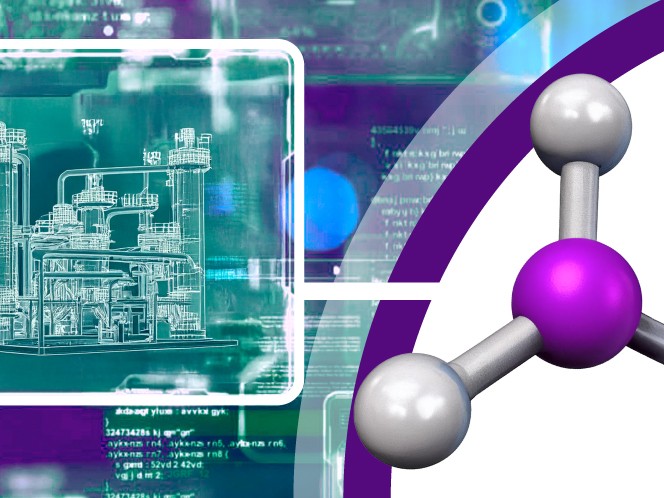
From food production to plastic, water purification to fertilizer, ammonia is all around us. It’s also set to be one of the key players in the industrial energy transition, meaning demand for ammonia is likely to increase over the coming decades. While nature produces ammonia through organic matter decomposition, since the beginning of the 20th century we’ve been using it in such large quantities that we must also produce it industrially. Traditionally, this is an energy-intensive process, which contributes 1-2% of the world’s carbon dioxide.
What is ammonia?
Before we get into how some companies are working to make ammonia greener, let’s explore the traditional process for synthesizing one of the most produced chemical commodities in the world. Ammonia is made up of nitrogen and hydrogen, both abundant elements on Earth. To create ammonia, we must combine them in a chemical process. Most current processes use large amounts of fossil fuel to convert nitrogen from the air and hydrogen from natural gas into ammonia. In fact, 98% of ammonia plants around the world use hydrocarbons for the hydrogen feedstock.
In order to increase our global supply of ammonia while continuing to reduce global carbon emissions, innovators are using industrial simulation software to develop new and greener processes for generating ammonia.
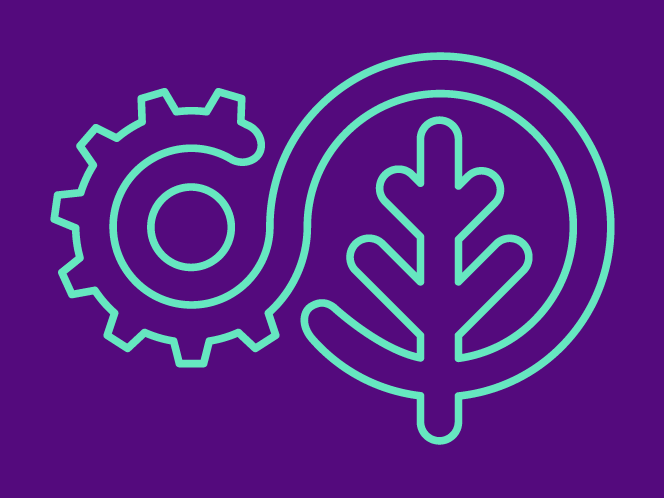
Our Industrial Life
Get your bi-weekly newsletter sharing fresh perspectives on complicated issues, new technology, and open questions shaping our industrial world.
AmmPower is one of those companies. The Toronto-based clean energy company builds modular green ammonia production units from its research and manufacturing facility in Michigan. The business focuses on providing modular ammonia production equipment that uses electricity and water instead of extracting hydrogen from fossil fuels.
Simulation software models a greener process
AmmPower recently developed a prototype for a carbon-free green ammonia production unit, which it calls the independent ammonia making machine or the IAMM unit. The IAMM unit contains several different components, including a part that extracts hydrogen from water rather than from hydrocarbons, one that separates nitrogen from the air, and the core technology—the ammonia synthesis loop, which creates ammonia using that green hydrogen and nitrogen. The machine uses a scaled-down version of the classic Haber-Bosch process.
AmmPower’s machine is the first of its kind, so the business needed to use new design and manufacturing processes. The AmmPower prototype is a small-scale version of its full-size IAMM machine, built to show potential customers how the process works. To create the initial, scaled-down prototype, the team began the design process with computer simulations using specialized software that could simulate chemical plant operations.
Engineers at AmmPower used industrial process simulation software to validate their designs by modeling how the physical variables such as temperature and pressure interact with each other. These interactions inform equipment design, piping layouts, and economic analyses. The simulations meant that AmmPower’s engineers could perform process design validation without spending money on parts to build multiple test units to trial. For example, engineers could easily test what would happen if they changed piping specifications within a simulation, something that would be very difficult and expensive on an already-built project. Simulations enabled the engineers at AmmPower to optimize their end design for cost, energy consumption and operating efficiency.
Detecting problems with a digital twin
AmmPower built simulations of both the startup and the steady state of the machine. After perfecting their simulations, the next step was to take the simulation output and turn it into a mechanical design. Engineers used 3D computer-aided design to make detailed component drawings and assemblies. Having trialed and tested several options virtually, AmmPower knew that its design would work before it began production.
Moving forward, the simulations will enable AmmPower to monitor its machines to help their customers operate and service the equipment. The original simulation model will evolve to act as a digital twin, providing real-time information about how a given machine is functioning.
Unit owners can collect their own data on process variables, such as temperature and pressure, so their operators can monitor and control the unit. Variations in those measurements would provide the first indication of a problem, allowing AmmPower to apply different tools to uncover what might be going on, and carry out maintenance if required.
In a recent episode of the Our Industrial Life podcast, Dr. Zhenyu Zhang, Chief Technologist at AmmPower, described the benefits of building this kind of digital twin: “[It] can really help us when we have the data to… use more advanced analytics and AI technology to help with the operation optimization, preventative maintenance, or other safety aspects”.
Lessons for the future
Because AmmPower will be able to gather data on how its machines are working, the accumulated knowledge will feed into future designs, taking us one step closer to a decarbonized future.
Meanwhile, industrial tech is powering several other companies’ modular ammonia projects. Fuel Positive’s green ammonia system, also at the pilot stage, is using industrial technology, including machine learning, to monitor, optimize and maintain its devices from a central location, easing the transition to new technology and simplifying updates. Atmonia’s nitrogen electrolyzer and Starfire Energy’s low-temperature ammonia cracking process are more examples of new, decarbonized ammonia production methods.
The wealth of new technological solutions coming from small businesses show how industrial simulation software can accelerate innovation. By easing the financial risks and fear around inventing new, decarbonized versions of industrial processes, technology can help companies model and scope the operational feasibility and potential economic impacts of different design scenarios. As technology makes easier and less risky for companies to investigate alternative and more sustainable ways of doing things, we have a better chance of moving industry into a sustainable and decarbonized future.