How to make green steel
Posted: October 21, 2024
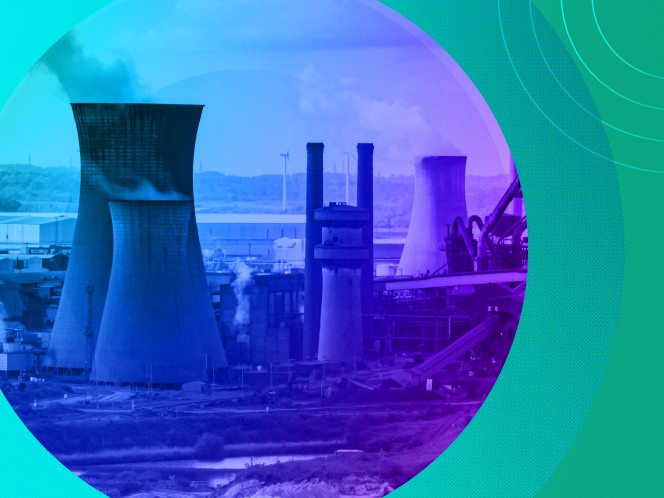
Steel is the most widely produced metal in the world. It is used in everything from cars, construction, kitchen appliances and the planes and cargo ships that deliver people and goods around the globe.
To give you a better sense of steel’s importance, iron ore, the key raw material in steel production, represents more than 90 percent of the metals mined annually. Approximately 98 percent of that iron ore is used in steelmaking. Nearly 19 billion metric tons of crude steel was produced in 2023.
But the prevalence of steel comes at a cost. The coal-intensive process that is most commonly used in producing steel results in 7 to 8 percent of global carbon dioxide emissions, among the highest of any sector.
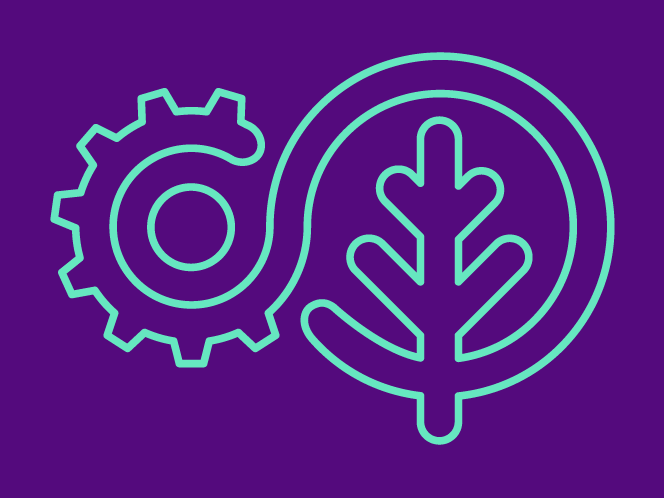
Our Industrial Life
Get your bi-weekly newsletter sharing fresh perspectives on complicated issues, new technology, and open questions shaping our industrial world.
As countries and companies try to lower their carbon footprint, finding a more environmentally-friendly, green method for making steel has emerged as a priority. According to the International Energy Agency (IEA), steel emissions would need to fall 50 percent by 2050 for the world to meet its climate targets. Over the same period, demand for steel is expected to rise between 30 and 55 percent.
In other words, the world needs to produce more steel while drastically reducing its carbon dioxide emissions at the same time. The most promising technology for meeting this goal is the introduction of hydrogen into the steel-making process.
How is steel produced?
To better understand how hydrogen may change the landscape of steel production, we need to take a quick look at how steel is currently produced. Although the history of steel dates back to the ancient world, the technological basis for today’s steel production was first innovated in the 19th century. Henry Bessemer’s process for reducing the impurities in iron revolutionized steel production and created the industrial world as we know it today.
In the most common method used today, iron is first produced in a furnace by mixing iron ore and purified coal, known as “coke,” which is then blasted with extremely hot air at fast speeds. The carbon dioxide emissions are created when carbon monoxide bonds with the oxygen atoms. The molten iron is then blown with pure oxygen in a separate vessel, further reducing its carbon content. The mixture is then ready to be placed into molds to cool into finished steel.
The introduction of pure oxygen is a latter innovation, first developed by Robert Durrer in 1948. His innovation drastically reduced the time needed to produce steel and remains the dominant method today. Around 75 percent of steel is still produced in coal-fired blast furnaces.
Can hydrogen decarbonize steel production?
One of the most promising technologies for reducing emissions is the use of hydrogen in the iron-making process instead of coke. Whereas coke reacts with the oxygen in iron to produce CO2, hydrogen bonds with this oxygen to form H2O, water. The smelt iron can then be converted to steel in an electric arc furnace (EAF), reducing carbon emissions by 95 to 100 percent.
EAFs could likewise serve as a bridge technology to emissions-free steel production. Steel has the unique property of being entirely recyclable. An electronic arc furnace produces fresh steel by melting down scrap steel without using coal.
This method has some limitations, however. The resulting steel is not suitable for all applications, meaning primary steel production is still necessary. Furthermore, EAFs require large amounts of electricity. If this is not powered by clean energy then emissions are still being produced upstream. Nonetheless, the direct carbon emissions at EAF mills are 90 percent lower than at mills using standard methods. They currently account for 30 percent of steel production worldwide.
Despite its promise, the adoption of hydrogen also faces challenges. The biggest problem is the availability of low-carbon hydrogen. Hydrogen needs to be stored and transported at very low temperatures or very high pressure, which is both costly and requires a large amount of electricity in its own right. If hydrogen were to account for 35 to 45 percent of global steel production by 2050, it is estimated that this would require more than double the total power production of EU member states in 2020.
There is currently only one facility devoted to producing hydrogen-based steel, the Hybrit project in Sweden. Nonetheless, Stegra is set to soon open the first large-scale hydrogen steel plant, also in Sweden, and the HBIS group in China (the largest steel producing country in the world) has begun producing hydrogen-based steel as well. Dozens of such projects are underway, including at ArcelorMittal, the second largest steel producer in the world.
Learn about how ArcelorMittal created an integrated remote operations center.
Though the challenge may seem daunting, the very history of steel production gives reason for hope. The basic oxygen process invented by Robert Durrer was developed on the margins of the steel industry. A decade and a half later, it was the dominant method of steelmaking worldwide.
His innovation was itself predicated on another invention a few years before: Pyotr Kapitsa’s turboexpander, which allowed for the industrial production of liquified oxygen. Innovations in the production and storage of hydrogen could similarly revolutionize steelmaking as we know it.