Recycling EV batteries is easy—refining the metals inside them is hard
Posted: January 17, 2025
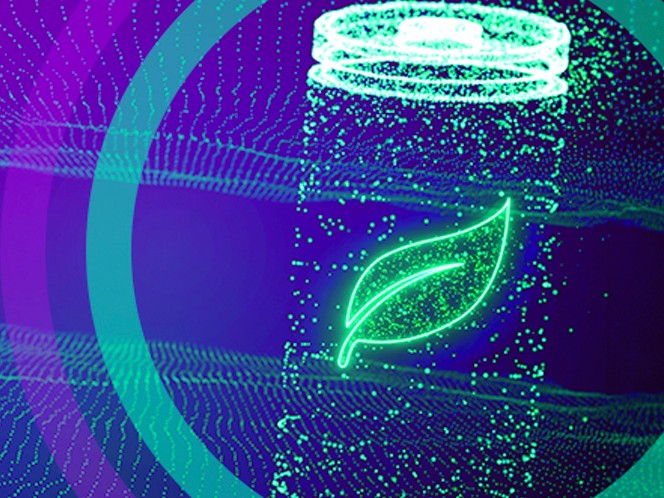
The world is building a lot of EV batteries. Global demand in 2023 was 850 gigawatt hours and is set to more than quadruple by 2030, according to research by the International Energy Agency.[1]
In the face of such growth, companies and governments around the world are understandably preoccupied with where, how and by whom all these new batteries will be made. But away from the headlines about gigafactory booms and gigafactory busts, lurk two major issues with battery production.
The first is the supply of the technology’s critical minerals—including lithium, copper, nickel, cobalt and manganese—which depends heavily on a small number of countries. The second is how to dispose of the avalanche of used batteries that will soon be rolling into scrapyards and landfills around the world.
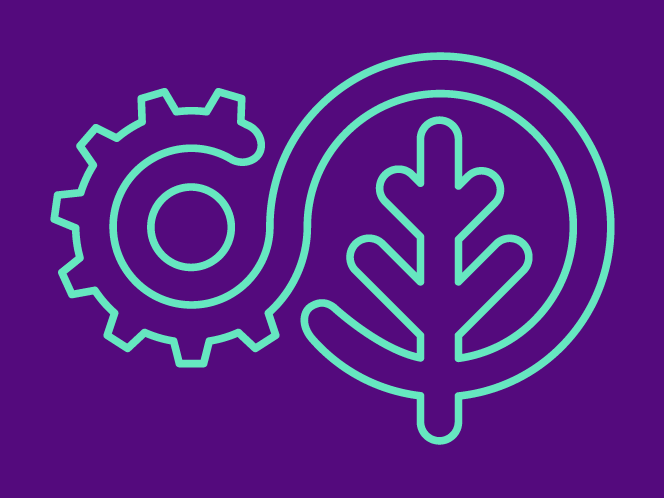
Our Industrial Life
Get your bi-weekly newsletter sharing fresh perspectives on complicated issues, new technology, and open questions shaping our industrial world.
An obvious answer to both issues would seem to be recycling: recovering and reusing the metals from old batteries could reduce waste and open up a new source of supply.
While that sounds straightforward in theory, the reality is not so neat. Used batteries may be collected and shredded locally, but the refining process—wherein metals are separated from waste and made ready for reuse—is largely done either in China[2] or in refineries attached to the very same mines in the very same countries that extract the metals in the first place. Plus, refining processes typically involve carbon-intensive smelting and chemically dangerous leaching.
At present, traditional recycling methods are addressing neither the environmental issues around battery disposal nor the attendant vulnerabilities of highly concentrated supply chains.
But all that is starting to change.
Recycle, refine and resell—all under one roof
In September 2024, a fine powder, aquamarine in color, began to tumble from a machine on an industrial site outside Cincinnati. The powder, a mixture of nickel and cobalt, is called mixed hydroxide precipitate (MHP), and it’s an essential material in lithium-ion batteries.
Until the machine in Ohio was switched on, precisely zero MHP was produced inside the United States. And the nickel and cobalt in this American-made MHP do not come from domestic mines (the US has only one nickel mine and no cobalt mines), but from recycled batteries.
The machine—called the Oyster—is the work of Nth Cycle, a start-up founded in 2017 off the back of research by its CTO Chad Vecitis and CEO Megan O’Connor. The Oyster is most easily understood as an extremely large, extremely sophisticated Brita filter. The so-called “black mass” of shredded batteries is pumped through layers of electrically charged carbon filters, which efficiently extract the desired metal.
This “electro-extraction” method is “a much more modular and greener solution than what you typically see for traditional refining,” O’Connor recently told Our Industrial Life.
That’s because—Nth Cycle’s facility in Ohio notwithstanding—the unique selling point of an Oyster is its potential to be installed in practically any recycling center or scrapyard, thereby making it possible to collect, shred and refine EV batteries on a single site.
“Instead of producing [critical minerals] with fossil energy and trucking them to one centralized facility to use,” explained O’Connor, “we have figured out a way to actually produce them with electricity—and we can do so right on-site, where the feedstock is.”
Indeed, by making it possible to refine batteries wherever they're collected—and to do so using electricity—Nth Cycle’s technology has the potential to improve the resilience and sustainability of critical mineral supply chains.
Whether technology like that of Nth Cycle is a match for the underlying—and implacable—economics of the recycling business is another matter.
When metals are cheap, recycling is expensive
Although a small number of countries produce the vast majority of the world’s critical minerals, those countries are producing a lot of them. Prices for the likes of lithium, nickel, copper, and manganese are low and appear set to remain so.
Low prices make extracting these metals less worthwhile—and sometimes not worthwhile at all, as mining behemoth BHP conceded when it announced the suspension of operations at its nickel mine in Western Australia.
The current market might seem inhospitable to new ventures, but O’Connor remains bullish on Nth Cycle’s prospects for a couple of reasons. The first is the MHP demonstration facility outside Cincinnati, which she says is proving viable even in this environment of low-cost metals. The second is the company’s toll-based business model, which sees it charge recyclers not for buying an Oyster but according to the weight of the waste they put through it.
The pricing system, combined with an Oyster’s on-site deployment, makes Nth Cycle a low-risk proposition for recyclers looking to get into the refining business: when prices make it worthwhile to refine their waste, recyclers can use an on-site Oysters; when prices are low, recyclers can wait for the market to improve without the stress of sunk costs and the pressure of expensive machinery lying idle.
Critical minerals are changing with technology
Given it is only a few years out of the lab and still reliant on venture capital funding, Nth Cycle’s long-term success is far from guaranteed—especially with vertically integrated recycling companies like Redwood Materials and Li-Cycle already operating at scale.
One reason for optimism around Nth Cycle, however, is the flexibility of its technology. The start-up claims a single Oyster system can extract practically any metal, with only the electrical charge of the filter needing to be altered.
Such adaptability could be particularly valuable in the context of the rapid advances in green technologies. Emerging lithium-sulfur battery chemistry, for instance, does not require many of the minerals the US and the EU currently consider “critical.”
Meanwhile, however, lithium-hungry gigafactories are sprouting up all over the world. McKinsey forecasts that, absent further investment in production, there will be a 55% shortfall in lithium supply by 2030, and the IEA reports that “the recycled input rate for energy transition minerals is much lower than that for other bulk materials.”[3]
Against such a backdrop—not to mention a rise in protectionist policies around critical minerals—it seems safe to bet that recycling will only become more important.
But for recycling to become a significant and reliable source of supply, refining technology needs to improve. Nth Cycle’s Oyster system appears to be offering a promising route forward, though only time will tell if the company is a true pearl.
[1] Report: Global EV Outlook, 2024, page 142.
[2] Report: Recycling of Critical Minerals, page 38.
[3] Report: Recycling of Critical Minerals, page 25.