Turning mine waste into profit
Posted: December 05, 2024
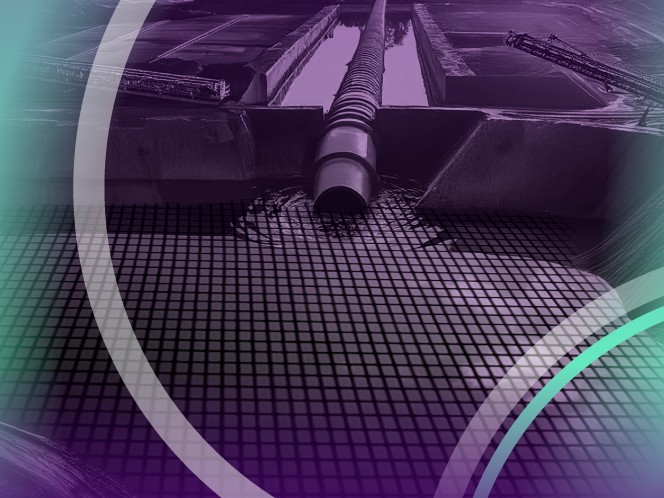
Mine wastewater is transforming from a costly problem to a valuable source of critical minerals. Mining often generates highly acidic wastewater full of sulfates and other dissolved metal salts. These metals leach into the water that mines use to suppress dust, cool equipment and separate out ore from minerals. Regulations require mines to clean the water from this acid mine drainage (AMD), but that process usually leaves an undifferentiated sludge of metals and other chemicals behind. As the metals in that sludge become more valuable, new technology is helping mines to recover valuable metals that they would otherwise be throwing out with the proverbial bath water.
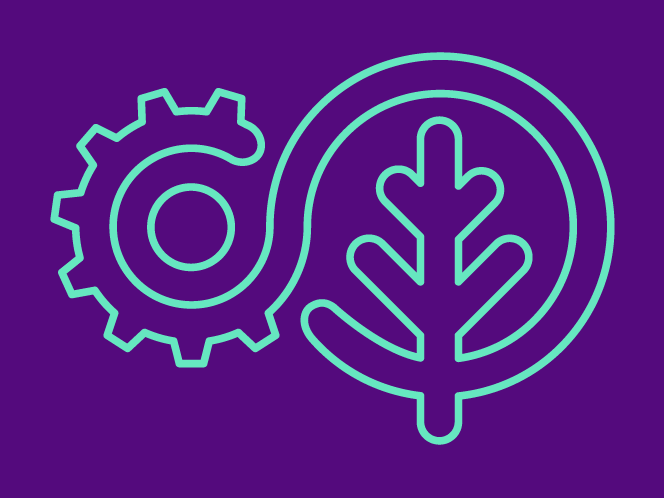
Our Industrial Life
Get your bi-weekly newsletter sharing fresh perspectives on complicated issues, new technology, and open questions shaping our industrial world.
How do mines process wastewater?
Standardly, mines have used chemical processes to precipitate out the metals dissolved in wastewater. The metals sediment into a solid mass that mines can then mechanically separate from the water. They store that sludge—called mine tailings—indefinitely in specially-built dams or pits.
Separating mine tailings from water is a costly process that doesn’t contribute to a mine’s revenue. It can require large outlays of both energy and expensive chemicals, and the end product is just a toxic sludge of jumbled metals that go to waste.[1] Many of those metals—such as copper, cobalt, nickel and lithium—would be extremely valuable if only they could be extracted and purified.
Several new technologies are aiming to do just that.
How does wastewater metal recovery work?
SiTration is a startup out of MIT that has developed a silicon filter that it can tune to selectively extract different metals. The company has partnered with Rio Tinto to research how best to apply the technology to mine wastewater. Over the next five to ten years, SiTration and Rio Tinto hope to develop a filtration unit that can process 100 cubic meters of water per hour.
The silicon filter holds up well to the high acidity of mining wastewater. SiTration can etch different sized pores in the filter that will selectively target different metals, such as copper, nickel, cobalt and platinum-group metals. Because silicon is a semiconductor, the company can pass different voltages across it, which further tune it to select for particular metals.
“We can produce membranes with pore sizes from the molecular scale up to the size of a human hair in diameter, and everything in between," the company’s co-founder and CEO, Brendan Smith, told MIT News. "Combined with the ability to electrify the membrane and separate based on a material’s electrochemical properties, this tunability allows us to target a vast array of different operations and separation applications across industrial fields.”
In addition to working with Rio Tinto to apply the technology to mining waste, SiTration is also exploring using it to recover critical minerals from metal refining and used electric vehicle batteries. Smith estimates that the technology could reduce chemical use by 95% for metal refineries.[2]
What technologies extract metals from wastewater?
The hope is that mines will not only reduce the cost of cleaning water but also generate more revenue from the minerals they isolate and recover from the filtering process. SiTration’s electro-filter technology is just one of several currently in development, including more conventional filters and bio-mining, which uses microorganisms to selectively extract minerals from wastewater. SiTration is betting that its ability to customize its filters will give mining companies the flexibility they need to extract—and profit from—a wide range of minerals that would otherwise go to waste.
References
[1] https://www.sciencedirect.com/science/article/pii/S2405844024007618#bib11
[2] https://techcrunch.com/2024/06/05/sitration-uses-silicon-wafers-to-reclaim-critical-minerals-from-mining-waste/