Using bacteria to turn post-consumer plastic into silk
Posted: September 20, 2024
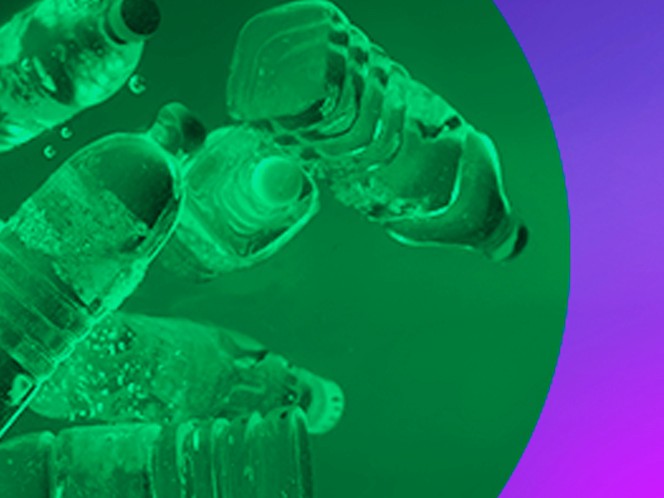
Since the 1950s, humans have produced more than 8.3 billion metric tons of plastic. Today, plastic is used in everything from critical medical equipment to food packaging, clothing, cars, computer equipment, and hundreds of everyday household items. But while plastic has become a critical part of our lives, much of the plastic produced globally every year ends up in landfills or the environment, where it slowly breaks down into tiny pieces. It can take thousands of years for plastic to degrade fully into its basic natural components.
Now, scientists are teaching bacteria to munch on discarded plastic and turn it into a new useful material: silk.
How plastic-silk production works
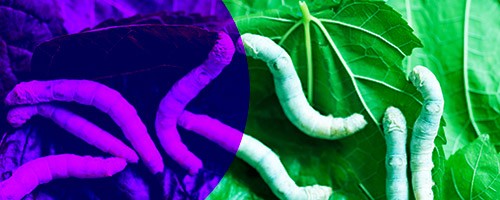
Researchers and industry leaders have been searching for a biological solution to break down plastic for decades. But interest surged in 2016 when a research team at Japan’s Kyoto Institute of Technology isolated a bacterial enzyme capable of breaking down polyethylene terephthalate (PET), a very common plastic used in textiles and packaging, with over 55 million metric tons produced each year globally.
Since then, researchers have isolated various plastic-degrading enzymes from bacteria and fungi. They either chemically synthesize these enzymes or engineer microbes like E. coli to produce them.
Recently, researchers at Rensselaer Polytechnic Institute in Troy, New York, succeeded in turning Pseudomonas aeruginosa, a nasty, multidrug-resistant bacteria naturally able to consume polyethylene into weavers of a new silk-like material. In a study published at the end of 2022, the researchers described how they genetically edited these microbes by inserting a sequence of amino acids similar to a protein found in silk.
The process is similar to brewing beer. Instead of feeding on sugars, the bacteria ferment a predigested form of plastic waste that has been pressure-heated. “It’s as if, instead of feeding the bacteria cake, we’re feeding it the candles on the cake,” Dr. Helen Zha, an assistant professor of chemical and biological engineering and one of the Rensselaer Polytechnic Institute researchers leading the project, said in a press release.
The resulting material is similar to the silk spiders use to spin their webs and could have applications in textiles, cosmetics and medicine.
“Spider silk is nature’s Kevlar,” Zha said. “It can be nearly as strong as steel under tension. However, it’s six times less dense than steel, so it’s very lightweight. As a bioplastic, it’s stretchy, tough, non-toxic, and biodegradable.” Such attributes make this new silk a great material for the future. Using the different types of silks spiders make as a source of inspiration, researchers can modify the bacteria-produced silk by tweaking the genes that encode specific proteins.
Microbes and the future of the plastics industry
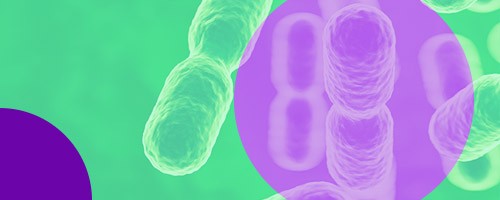
French company Carbios was the first to launch a PET-eating enzyme commercially. The company isolated the enzyme from bacteria in compost and later modified it to improve efficiency.
The enzymatic reaction breaks PET down into its main constituents: terephthalic acid and ethylene glycol. These constituents can then be used to produce new plastics without losing material value associated with traditional recycling approaches.
Carbios announced plans to open the world’s first industrial-scale enzymatic PET biorecycling plant in Longlaville, France, in 2022. The facility will commence operations in 2025 and will be capable of processing 50,000 metric tons of post-consumer PET waste annually, which equates to around 2 billion PET plastic bottles.
However, transforming plastic into a biodegradable material like silk, rather than plastic again, could be even more beneficial, potentially revolutionizing manufacturing processes. “What’s really exciting about this process is that, unlike the way plastics are produced today, our process is low energy and doesn’t require the use of toxic chemicals,” Zha said. “The best chemists in the world could not convert polyethylene into spider silk, but these bacteria can. We’re really harnessing what nature has developed to do manufacturing for us.”