Why predictive maintenance is key to a renewables-reliant grid
Posted: December 20, 2024
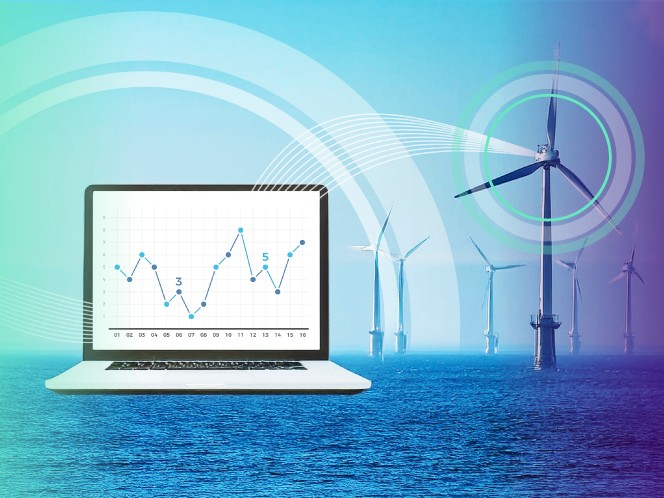
On the Dogger Bank, a large sandbank in a shallow part of the North Sea, ships have been laying the foundations for what will be the world’s largest offshore wind farm, a vast field of 277 turbines across an area nearly twice the size of New York City.
Physically getting out there is no easy feat. The wind farm is located some 130 kilometers from the nearest port and the top of each turbine, where the drivetrain is located, towers more than 100 meters above the sea. And then there’s the weather.
The logistics illustrate why maintaining a power plant can be significantly harder now than it used to be, when utilities only had to contend with large, centralized power stations on land. And it’s one reason why companies in the sector are increasingly turning to predictive maintenance to make sure their plants keep running.
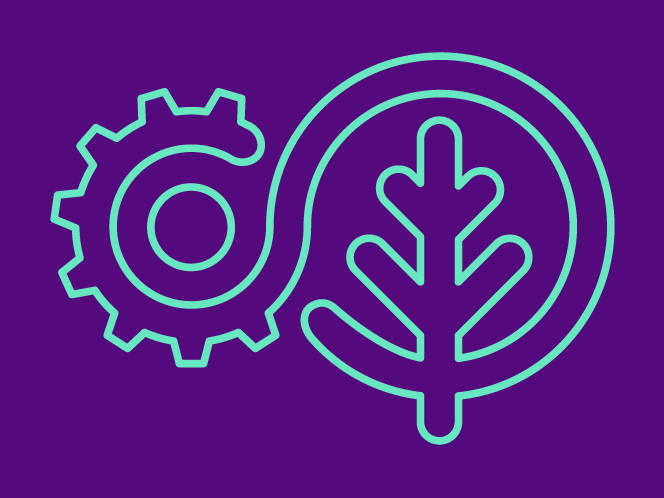
Our Industrial Life
Get your bi-weekly newsletter sharing fresh perspectives on complicated issues, new technology, and open questions shaping our industrial world.
Why is predictive maintenance gaining ground in renewable energy?
Wind turbines are complex machines with thousands of parts. Their long list of potential issues range from blade damage to generator failure; even the lubrication and filtration systems in a turbine’s gearbox can cause an outage.
For operators, this can quickly get expensive: Ever-larger turbines also mean higher potential losses from unplanned downtime. Meanwhile, older wind farms, while smaller, are more likely to show wear and tear from years in operation.[1] And even onshore farms are often located in remote areas, making regular maintenance visits difficult and costly.
To facilitate predictive maintenance, utilities including E.ON and Enel are installing sensors on their turbines to measure everything from temperature to vibration, wind speed to output. A machine-learning algorithm then uses the data they collect to spot patterns and anomalies—like unusual vibration in the gearbox, which could mean that a bearing is wearing out—so that a maintenance crew can be dispatched to fix the issue before it becomes a serious problem.
Spotting faults early has a host of other benefits besides increasing availability and performance. It can help companies better manage staffing and spare parts, and even cut the need for backup power reserves.
Australian utility AGL Energy already undertakes advanced pattern recognition monitoring for each of its wind turbines, as well as its solar, hydro and gas plants. In total, the company runs 3,500 models predicting 52,000 data points at five-minute intervals, saving AU$6-7 million per year as a result, according to David Bartolo, AGL’s head of asset intelligence.
“The more rich history you have at the higher resolution, the better the understanding of where you are. You can understand where your asset is right now,” Bartolo told Our Industrial Life last year. “And then when you can see those deviations from normal behavior, you're picking up failure modes earlier than any other technology can provide.”
How is AI improving predictive maintenance?
AI is set to further enhance the efficacy and accuracy of these systems, since it can analyze vast amounts of information and, crucially, learn and refine its analysis over time as it digests more and more data.
That works particularly well for renewables, according to Kristjan Jansons, chief executive of Estonian AI startup MindTitan. “Wind turbines are suited to predictive maintenance because they are standardized. AI likes to generalize based on a large amount of data,” he says.
According to Deloitte, using AI models becomes particularly helpful when predictive maintenance procedures draw on a broader array of data. Aside from sensors, that can also include historical maintenance and repair logs, production data, procurement and enterprise resource planning data, as well as reports from workers in the field. AI can even help prioritize any maintenance jobs that need to be carried out.[2]
“In a way, the AI solution could serve as an omnipresent maintenance employee helping the human workforce make better decisions about when and where to target operations,” Deloitte says.
For utilities, AI can have much broader applications beyond just maintenance. Indigo Advisory, a consulting firm, says there are more than 50 possible uses for it in the wider energy sector, from renewables—creating a market worth up to $13 billion—to helping select the best sites for wind and solar farms and forecasting electricity demand.
Predictive maintenance beyond power generation
When it comes to predictive maintenance, power companies have also expanded applications to newer parts of their businesses, like electric vehicle charging points.
Although more generally accessible for maintenance than wind turbines, the number of electric charging points is growing quickly. Europe alone could have 3.5 million by 2030—a vast fleet of assets to monitor.
“There are tasks where artificial intelligence is simply better at processing [a] significant amount of data,” says Stefan Herr, a senior manager at E.ON’s innovation unit. “It can make connections, recognize patterns and make predictions much better and faster than any human service team, no matter how large or experienced, ever could.”
Something AI is terrible at, though? Scaling a 100-metre-tall turbine in the middle of the North Sea.
References
[1] https://shoreline.no/new-report-larger-turbines-and-aging-assets-pose-fresh-challenges-for-offshore-wind-om/
[2] https://www2.deloitte.com/us/en/pages/consulting/articles/using-ai-in-predictive-maintenance.html