Amcor, a global leader in developing and producing responsible packaging, was already capturing a lot of data from its 23 facilities with a traditional SCADA system. But a lack of visibility, standardization, and automation meant the company wasn’t getting enough value out of that data. In order to drive better line performance, Amcor built a manufacturing execution system suite at the edge using AVEVA System Platform to enable teams to consistently measure and track production data.

Challenges
Lack of visibility into operational data
Manual data sharing and reporting led to inaccurate information
Micro-stops and other downtime events led to production losses
Results
2%
improvement to overall equipment effectiveness
3%
faster production cycle

increased visibility of equipment efficiency and changeover effectiveness

gained full visibility of asset utilization and energy performance

created a standardized structure for data to support analytics and AI
Beyond the buzz
Advanced tools like AI, digital twins, and predictive analytics are buzzy industrial tech these days—but what are more modest solutions that still help companies operate more efficiently? How might leaders drive better equipment performance in line with their organization’s specific business goals, as opposed to simply reaching for the new and shiny? As Carlos Peredes, Automation Manager at Amcor, says, “Let’s talk about what regular mortals can do.”
Amcor, a global leader in developing and producing responsible packaging, already had a traditional SCADA system for its 23 facilities that was capturing a lot of data. The problem was the company wasn’t getting enough value out of that data. There was a lack of visibility, standardization, and automation. Operators were still grabbing a piece of paper to record SPC levels. Manual data sharing and reporting were slowing down operations and leading to inconsistent or incorrect information. Everyone was working on the same solution—trying to calculate OEE—but they were going about it in different ways. Operators were creating different objects and templates and visualizations. Ultimately, these disparate approaches led to data silos and inefficient operations.
“We were just capturing a tremendous amount of data, putting it into our historian, and there was a very minimum value.”
—Carlos Peredes, Automation Manager, Amcor
Solution
Amcor deployed AVEVA™ Manufacturing Execution System and AVEVA™ System Platform to improve real-time visibility of production data and increase equipment efficiency.
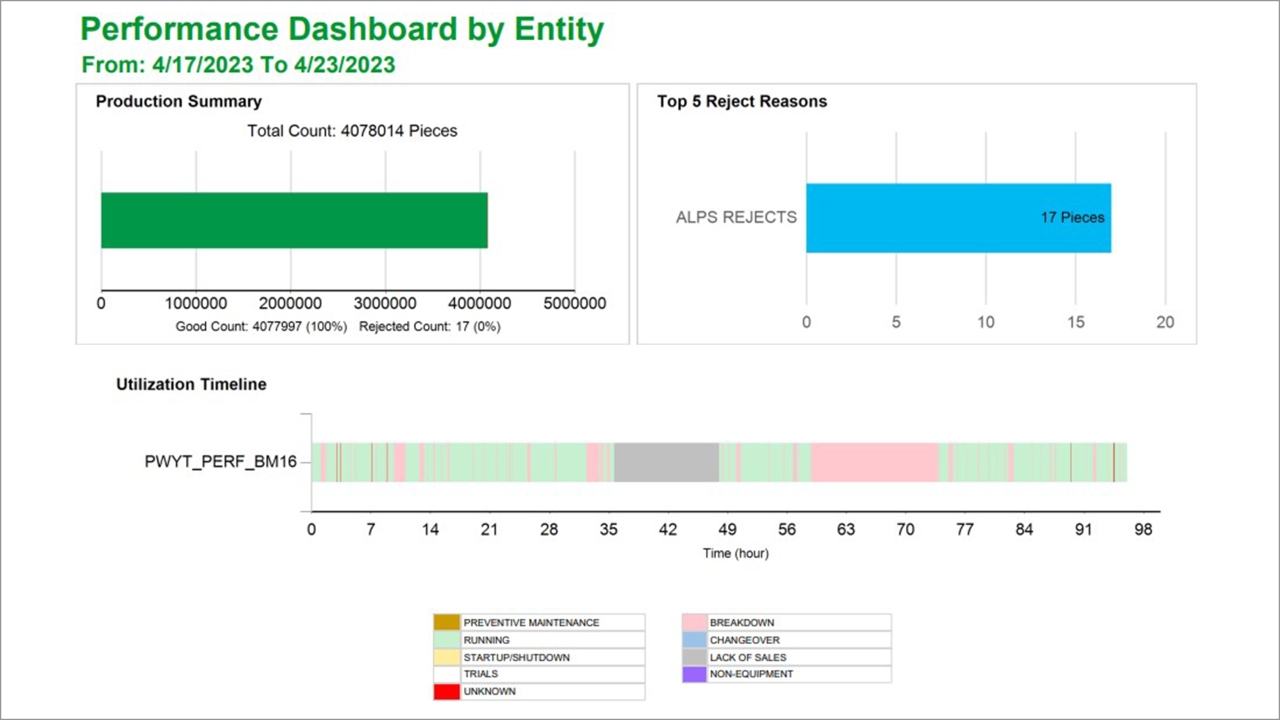
Building a foundation to improve efficiency
Amcor develops and produces responsible packaging—both rigid and flexible—for food, beverage, pharmaceutical, medical, home, personal care, and other products. It operates out of 218 sites worldwide in 41 countries. The CEO of Amcor has committed to develop all Amcor packaging products to be recyclable or reusable by 2025. To reach this target and deliver sustainable packaging at a minimum cost, Amcor needed to find new ways to drive better line performance.
Taking OEE as their primary metric, Peredes and his team set out to build a standard for how to measure line performance consistently across their plant facilities. First, they consulted with the company’s current SCADA control users to see how they were using the current system and what they needed to operate more efficiently. They wanted to involve the company’s own operators and engineers to nurture and grow internal talent and expertise, putting the right tools in operators’ hands without taking the fun away from in-house system engineers.
The result was what Amcor—with a nod to AVEVA’s solution of the same name—calls “Unified Operations.” Peredes and his team used AVEVA Manufacturing Execution System on top of AVEVA System Platform, formerly used as a traditional SCADA system, to build an MES suite at the edge that integrates with their PLCs. This layer of MES enabled teams to consistently measure and track production events data. They created metrics that combined energy efficiency data with production counts to finally get a meaningful measurement of energy performance. Performance dashboards contained validated real-time data, providing complete visibility of asset performance.

Improving OEE with real-time performance data
There are two main activities Amcor looks at when measuring production efficiency: injection molding and blow molding. The company had been losing money by not being able to detect cavitation and monitor how plants were blocking cavities. Operators were seeing a lot of variance in cycle time. If a machine is producing 96 parts per ten seconds, say, and machines have cavitations of ten parts blocked, that adds up at the end of the day. By being able to look at cycle time variance against a standard of how the machines should be performing, operators are now able to see when those metrics are off and work to identify and solve the issue. Overall, Amcor has seen a 3% improvement in production cycle time by looking at this real-time cavitation data.
Another efficiency metric Amcor looks at is micro-stops in blow molding. When the company was operating mainly with manual recording, operators weren’t tracking every second of a machine’s micro-stops, which meant that downtime data wasn’t accurate. Over the course of a shift, a machine might have 45 minutes of micro-stops. Again, that time adds up. Being able to see that downtime accurately captured automatically every 20 seconds, maintenance teams can now address issues and gain quick wins in efficiency. Using this system, the company improved OEE by 2% through capturing these micro-stops in blow molding.
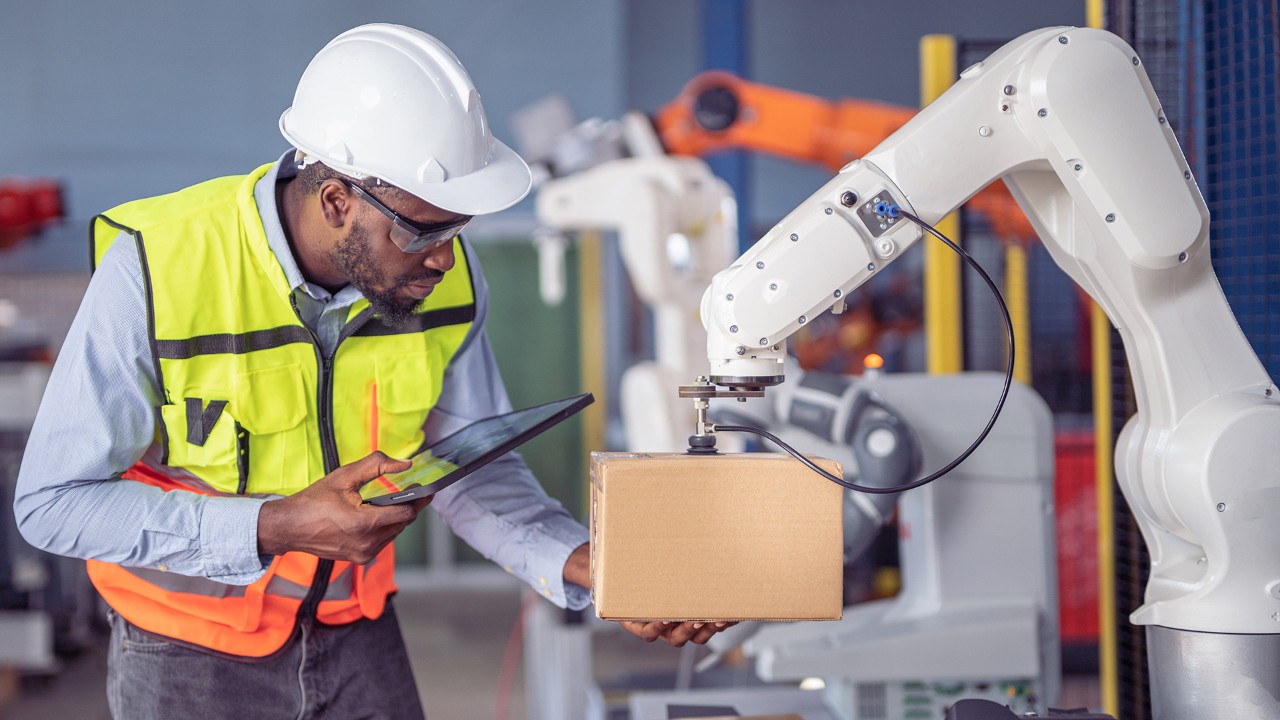
A data foundation to drive growth
Amcor now has a unified interface to manage scheduled and unscheduled downtime. It captures every stop from machines, which increases machine performance and quality of its packaging. Operators can be held accountable for downtime events, since real-time performance data is being captured at the edge and visualized. Preventive maintenance and changeover effectiveness has increased. With full visibility of asset utilization and energy performance, operators can make sure that when new lines come in, they’re SCADA-ready and run consistently based on the platform’s efficiency metrics. The commissioning of new assets is automated and standardized, too.
Operators no longer present disparate, inaccurate data. Standardized nameplates, naming conventions, graphics, and user interfaces ensure that everyone’s speaking the same language. This standardization makes it easier to incorporate new digital tools like analytics and AI. They’ve now defined an architecture for enterprise reporting and analytics. Training and nurturing internal competencies are built into this approach as well. Any time a new operator or engineer comes onboard, they are trained on the same tools, and everyone can drive continuous growth in how these tools are used.
“Every time there’s a new order, we track that order. We feed it into our SCADA system. We track what the standard should look like, and then we tie it to the machine to see how we’re running against the target.”
—Carlos Peredes, Automation Manager, Amcor
The Amcor team might be made up of mere mortals, but they now have an ERP system that integrates and optimizes production processes based on standardized real-time data visibility. They’ve built a sustainable program that will allow them to grow their business at their own speed, utilizing internal competencies as well as leveraging the expertise of partners like AVEVA. With this new foundation, Amcor is well on its way to meeting its sustainability objective to be completely recyclable by 2025—good news for all mortals.
Product highlights
Formerly Known As Wonderware MES
Maximize profitability, flexibility, quality, and compliance in manufacturing by digitally managing the rules and information for all operational activities and plant events in real-time. A work process-centric and Model-driven approach reduce the time to value and cost of ownership for both plant deployments and multi-site MES rollouts.
Empowering you with a responsive control platform for supervisory control, HMI, MES, and IIoT.