To help biofuel producers enhance renewable diesel production, ExxonMobil implemented technology ExxonMobil Renewable Diesel (EMRD). Using AVEVA PRO/II Simulation, ExxonMobil developed EMRD, which later they incorporated into Strathcona renewable diesel facility, which produces 20,000 barrels of fuel a day, making Strathcona the largest renewable diesel facility in Canada. This new facility is expected to help the Canadian transportation sector reduce its CO2 emissions by 3M metric tons a year.
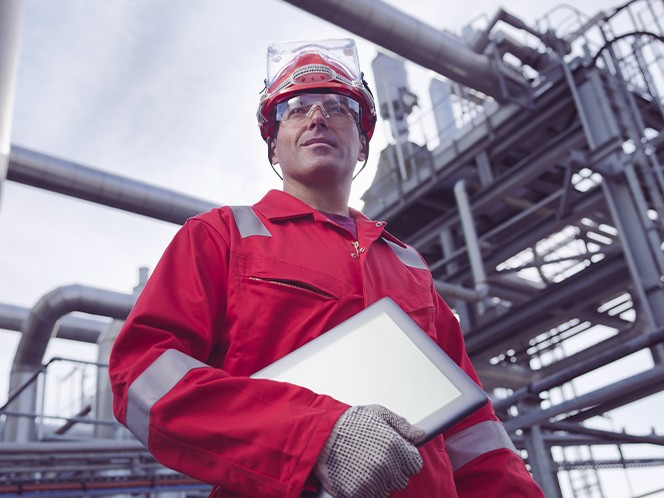
Challenges
Producing new, sustainable fuels to meet the world’s energy needs
Sustainable fuel producers must meet advanced cold flow specifications while maximizing yield
Optimizing different variables in the renewable diesel process, such as operating temperatures and feed stage locations, requires advanced, customizable simulation tools
Results

The new ExxonMobil Renewable Diesel (EMRD) process provides superior control, optimizing production while meeting rigorous product specifications.
20,000
barrels of renewable diesel per day expected at the Strathcona diesel facility using EMRD
3 million
metric tons of CO2 emissions reduced per year at this facility
ExxonMobil Renewable Diesel (EMRD)
The transportation sector produces about a quarter of the world’s CO2 emissions. And while the necessity and urgency of climate action is intensifying, our need to transport ourselves, goods, and services isn’t going anywhere. The global population will continue to rise and with it so will our need for transportation and our demand for energy.
That’s why the oil and gas leader is charting a new path with ExxonMobil Renewable Diesel (EMRD), a proprietary process technology designed to help biofuel producers enhance renewable diesel production while meeting stringent product specifications. To design and optimize EMRD, ExxonMobil relied on AVEVA™ PRO/II Simulation.
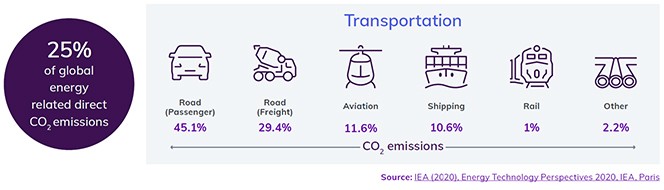
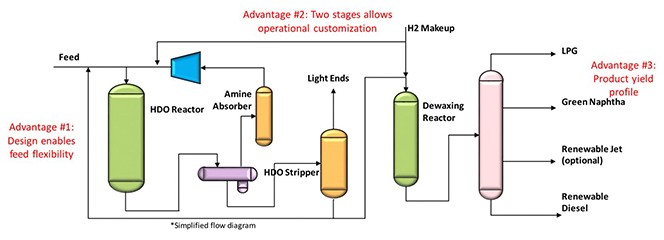
New, sustainable fuel sources demand new processes
“Growing sustainable fuels is going to require a lot of new processes,” says Dr. Trivedi. “And so, the question becomes, how do I go about synthesizing that new process?” The answer is: with careful attention to detail and advanced simulation tools. Here’s what process synthesis looks like in a nutshell: the first step is identifying the chemistry that will transform your feedstock (in this case, canola oil) into the desired product (renewable diesel). And once you have the chemistry, the next step is finding a catalyst to hasten the reaction so that you can achieve commercially viable continuous production. After that, it’s time to design the reactors, which will turn that feedstock into product.
At this stage, besides product, your reactors will be producing byproducts that you don’t need, and you’ll likely end up with some unreacted feedstock as well, which means it’s time to design the separation synthesis phase of your process.
The byproduct must be removed, and the unreacted feedstock must be recycled into the reactor to avoid loss of yield. Having accomplished this much, you now understand the operating parameters of your reactor (pressure, temperature, flow, etc.), and you’re ready to harness all that information to design the heat exchange network. Next, you design the utility system, which tells you, at the refinery gate or the unit gate, how much power you’ll need to import, how much fuel, steam, and so on. Finally, you turn this all into P&IDs, leave the simulation and start building.
Designing and optimizing each of these phases of the process is incredibly complex and requires sophisticated simulation technology. That’s where AVEVA PRO/II Simulation comes in.
Solution
AVEVA PRO/II Simulation, a steady-state simulator that optimizes plant performance by improving process design, operational analysis, and performing engineering studies.
Turning chemistry into process
“Renewable diesel chemistry is well known and understood,” says Dr. Trivedi. But understanding the chemistry is not the same as using that chemistry to produce 20,000 barrels of renewable diesel a day. Using AVEVA PRO/II Simulation, ExxonMobil developed its advanced processing technology, EMRD. Unlike other renewable diesel production processes on the market, which are commonly one-stage processes, EMRD happens in two stages. Hydrotreating and dewaxing are controlled separately, which gives biofuel producers the superior control they need to meet advanced cold flow properties while maximizing their yield. With added refraction, EMRD can also produce sustainable jet fuel as a secondary product.
The predominant component of the bio feedstock—vegetable oil or used cooking oil—is triglyceride, a molecule made up of three glycerides connected at one end. This is the same triglyceride found in your blood, Dr. Trivedi notes. ExxonMobil uses EMRD to convert these triglycerides and hydrogen into n-paraffins, as well as propane, water, carbon monoxide, and carbon dioxide. N-paraffins, or normal paraffins, boil in the same region as diesel and jet fuels, but there’s a problem still; as the temperature drops, these paraffins begin to solidify. “You definitely don’t want that to happen to you at 30,000 feet,” says Dr. Trivedi.
Using AVEVA PRO/II Simulation, the team ensures that the renewable diesel it’s producing meets the properties of conventional fuel. One possible solution is to break these long, heavy carbon molecules up to improve the poor cold flow properties of n-paraffins. This strategy, however, reduces yield. With AVEVA PRO/II Simulation, ExxonMobil designed a process to convert paraffins into iso-paraffins, which preserves yield while improving the resulting diesel’s cloud point, which is the lowest temperature at which crystal formation in biodiesel can be observed as a cloudy suspension.
“Having multiple ways of predicting things in the simulator helps you quickly identify the bookends and therefore come up with a robust design.”
—Dr. Kirtan Trivedi, Global Projects, ExxonMobil
Essential tools for optimized process designs
From designing the reactors and the quench system to optimizing the heat exchanger network via pinch analysis, the process to produce renewable diesel is incredibly intricate and complex. With AVEVA PRO/II Simulation, ExxonMobil had the advanced simulation tools it needed to simplify the process. As a result, the team reduces model-building and computation time and improves their fundamental understanding of how the model works and how its components interact.
Another advantage of AVEVA PRO/II Simulation is the ability to embed component properties from your own plant data into the simulation. With AVEVA PRO/II Simulation, Dr. Trivedi says, ExxonMobil can find the ‘bookends’ of the design model by incorporating different flash-point calculation methods into the simulation, which ensures the team creates a high-quality design. This is critical, Dr. Trivedi says, to make sure the system hydraulics can handle the products ExxonMobil produces. “Once you put steel to ground,” says Dr. Trivedi, “you don’t want one of these things to limit you in terms of maximizing your profit.”
Conclusion
Now that ExxonMobil has synthesized and optimized its EMRD process technology with AVEVA PRO/II Simulation, it’s time to leave the simulator, and, as Dr. Trivedi says, “Put our money where our mouth is.” As part of the company’s plan to invest approximately $17Bn in lower-emission fuel initiatives by 2027, ExxonMobil will incorporate its EMRD technology into Imperial’s Strathcona renewable diesel unit. The refinery will use locally sourced canola oil as feedstock to produce an expected 20,000 barrels of fuel a day, which will make Strathcona the largest renewable diesel facility in Canada. Once operational, estimations suggest this new facility could help the Canadian transportation sector reduce its greenhouse gas emissions by approximately 3M metric tons per year.
Product highlights
AVEVA PRO/II Simulation – The Trusted Steady-State Process Simulator
Formerly Known As PRO/II Process Engineering
A simulator that optimizes plant performance improves your process design and operational analysis by performing engineering studies.