Mitsubishi Heavy Industries (MHI) has committed to becoming carbon neutral by 2040—an ambitious goal, but one the company knows is vital to ensure a more sustainable future. With AVEVA™ PI System™, MHI has created a smart data infrastructure that connects humans and machines, automating and optimizing across the thermal power life cycle and other business areas, including factory optimization and data center decarbonization.
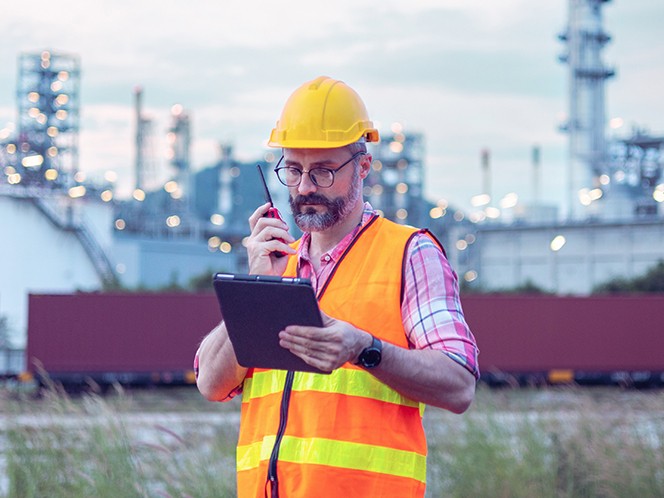
Challenges
Committed to carbon neutrality by 2040, which requires decarbonizing factories and energy sources
Needed better visibility, analytics and optimization across its scope 1, 2 and 3 emissions
Geographically dispersed remote monitoring systems
Results

Monitoring and analysis of all thermal power plants with 24/7 customer support across four remote monitoring centers

Protected mission-critical data coming from customers and operating sites

Developed various ways to reduce carbon emissions and on track to be carbon neutral by 2040
Digitalizing the entire plant life cycle
AVEVA PI System has already helped MHI optimize and decarbonize its factories, energy sources, and processes across its value chain. The company has now expanded its application of AVEVA PI System in TOMONI, MHI’s proprietary suite of intelligent data solutions. With remote monitoring, advanced digital control systems, predictive analytics, and multi-layered cybersecurity, the company and its customers can optimize their power plant operations and decarbonize across the total plant life cycle—from construction to after-sales service.
MHI has four TOMONI HUBs, global remote monitoring centers that offer analytics services with 24/7 customer support. During start-up, load operation, and shut-down, TOMONI supports and guides decisions for customers to maximize profit and realize optimized operations and maintenance. The system’s AI simulation technology helps operators respond quickly to changes in the environment, equipment issues, and fluctuating market demands
"During COVID 19, we had a very difficult time dispatching our engineers and field workers to the site, especially abroad. Thanks to AVEVA PI System, we have performed remote site commissioning remotely from Japan to, for example, Indonesia, or Malaysia. And not just monitoring. We are providing wave applications for customers with our remote monitoring center.”
— Hiroyasu Ishigaki, Digital Strategy Chief Manager, Mitsubishi Heavy Industries, LTD.
From edge to cloud: A robust data infrastructure
From edge to cloud: A robust data infrastructure MHI collects data at the edge and moves it to MHI’s information and communication technology (ICT) platform, then gathers, analyzes, and visualizes the data with AVEVA PI System on Microsoft Azure, making this data available for users anytime, from anywhere. So far, TOMONI has over 145 connected plants, with over 680,000 data points and 24,000 visualization screens with AVEVA™ PI Vision™.
Through TOMONI, MHI can leverage its own expertise as OEM and offer operating assistance using AI and machine learning such as control valve diagnosis, combustion tuning, manual valve operation guidance, foreign object management, and inspection guidance. Users have secure access to data visualizations and custom alarms with 24-hour operational support in a Python execution environment with Power BI Reports. All this data infrastructure combines seamlessly to enable users to transform raw data into meaningful insights, with advanced edge and cloud security to ensure safe plant operations and the protection of customer data.
Solution
Mitsubishi Heavy Industries expanded AVEVA™ PI System™ use across all its activities, including the entire thermal power lifecycle, carbon capture and storage, factory optimization, and data center decarbonization.
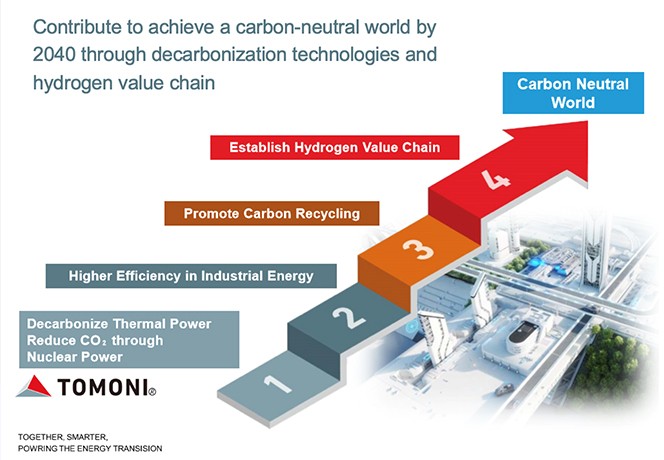
Commercializing carbon-free power generation with smart data solutions
Takasago Machinery Works is MHI’s gas turbine headquarter. Pivotal for carbon neutrality, MHI’s gas turbines are designed, manufactured, and validated using TOMONI within a unique facility that includes a 156 MW power station. The company is moving toward the goal of commercializing carbon-free power generation using hydrogen. To this end, it has achieved 50% mixed hydrogen firing during combustor tests—surpassing targets set by the European Green Deal—and aims for 100% hydrogen firing by 2030.
With high production costs, difficult storage and transportation, and market uncertainty, getting hydrogen is a challenge. To address this challenge, MHI has integrated hydrogen generation and storage in its Takasago Hydrogen Park in Takasago Machinery Works. Since beginning operations in 2023, this one-stop shop has validated technologies like water electrolysis, turquoise hydrogen (hydrogen obtained through pyrolysis of methane into hydrogen and solid carbon), and SOEC (solid oxide electrolyzer cell), all using TOMONI’s advanced data analytics and visualizations. This hydrogen solutions ecosystem positions MHI to lead carbon-neutral power generation, expanding next-generation hydrogen production technologies.
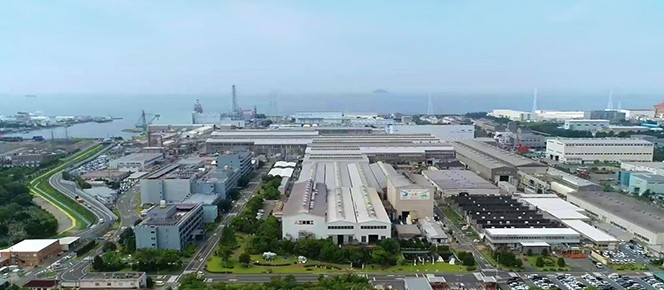
Capturing CO2 and optimizing factory operations
With so many facilities coming together for MHI’s new energy mix—hydrogen gas turbines, hydrogen generators, batteries, wind turbines, PVs—the stability of the power grid can become an issue. Solar and wind power generation are particularly variable, so energy from MHI’s gas turbines is required to ensure stability. The company developed an energy management control system using AVEVA PI System data collected at the edge and combined with AI-infused analytics in the cloud. MHI combines predictions about factory demand along with other factors like weather, power rates, fuel price, gas turbine performance, PV output, and battery health to create an optimization plan that maximizes efficiency of these different systems and minimizes carbon output.
MHI is integrating maintenance data with generative AI across the company, and one use case is a CO2 capture system. Monitored with AVEVA PI System, the capture system, spanning small and large facilities, has captured up to 5000 tons of CO2 per day. In expanding the use of its AVEVA PI System, MHI is also using the system to optimize factory operations and workflow. It gathers and processes machine data through PLCs to an AVEVA™ PI Server, then analyzes that data, combining it with other data, visualizing it, and improving processes by performing downtime analysis and predicting maintenance needs of equipment.
Smarter connections across all domains
MHI’s expanded AVEVA PI System contract now encompasses all MHI activities, facilitating smarter connections across its domains. In its new digitization project ΣSynX (Sigma Syncs), the company is combining intelligence and technology to enable coordination between humans and machines. For example, MHI is commercializing automated guided forklifts (AGF) and natural refrigerant chillers for increased automation and decarbonization. The company is combining this kind of automation with advanced plant monitoring, advanced cyberattack software, and intelligent video surveillance. And all this system data is centralized and easily available thanks to the single source of truth provided by AVEVA PI System.
One of the new growth areas MHI is piloting is data center decarbonization. Data centers consume a lot of power. Cooling systems are vital to keep them running, and it’s important to make sure these cooling systems run as efficiently as possible. So MHI is using Sigma Syncs to provide high-efficiency AC and power generation systems for hyperscale data centers and working on proof of concept for micro-data centers, challenging because of the small footprint and high density of these centers, which require more nuanced data-driven optimization.
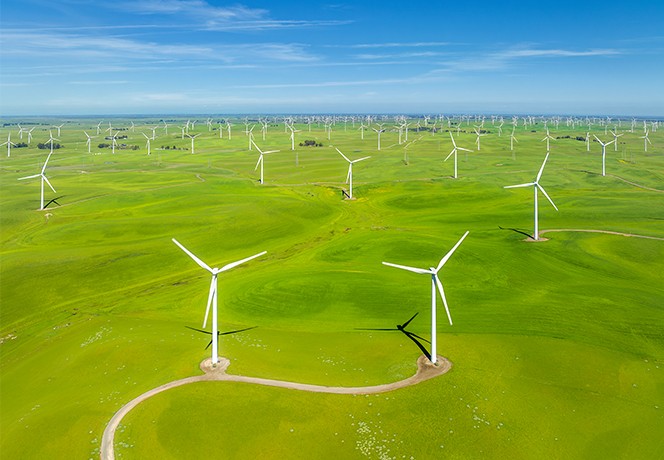
A sustainable future for all
MHI is harnessing best-in-class technology combined with human intelligence to provide one-stop service to customers and help everyone on their digitalization journey work smarter and more efficiently. The energy transition demands a new, more connected way of optimizing processes and handling the complexity and variability of new energy resources across both the supply and demand sides of the power equation. “TOMONI” is a Japanese word meaning “together with,” which perfectly encapsulates the collaborative, innovative, data-driven approach that MHI is taking, one necessary for a sustainable future for all of us.
Product highlights
AVEVA™ PI System™
Collect, aggregate, and enrich real-time operations data for immediate problem-solving and easily deliver formatted data to enterprise applications and advanced analytics.
AVEVA PI Vision
With AVEVA PI Vision, turn raw data into rich, visual displays and share valuable insights across your enterprise.