Nestlé is committed to empowering its people to think creatively about how to solve problems and push products to new heights. In this spirit of innovation, Nestlé partnered with AVEVA to optimize the production of its powder beverage products Nesquik and Ovaltine. With AVEVA, Nestlé designed a solution that uses real-time production data and advanced analytics to limit variability. This process improvement consistently yields a lower-density, and fluffier powder.
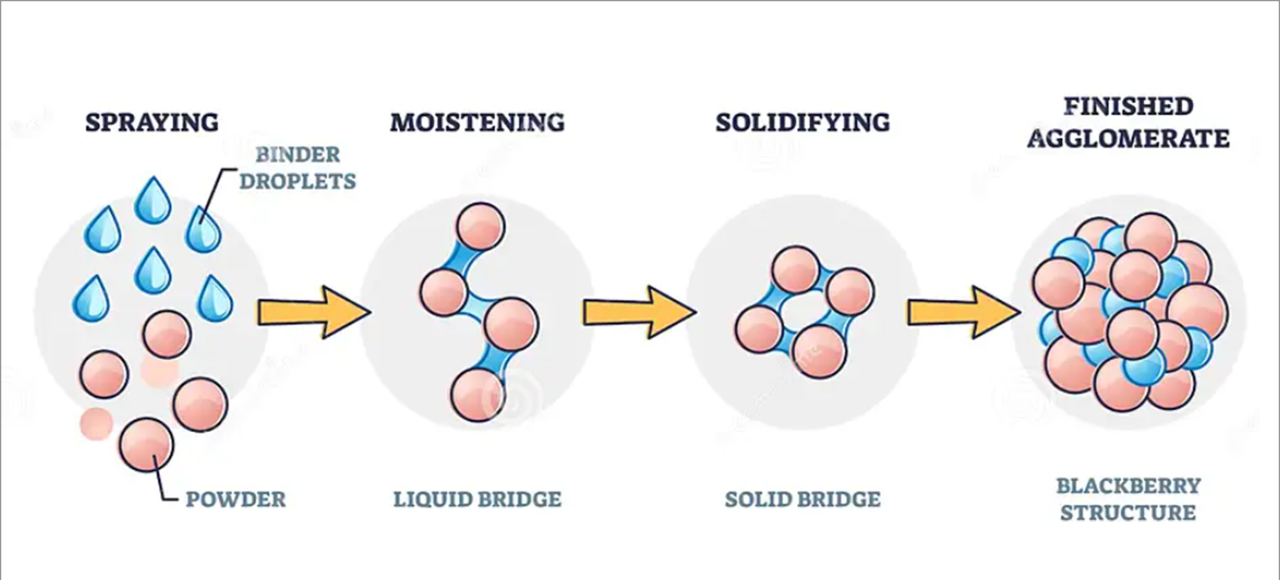
Challenges
Manual processes caused variability in product moisture and density
Low product yield due to low moisture
Inconsistent product caused unnecessary waste
Results

less product waste on production and packaging lines
101g
powder saved from every 1kg jar

consistently tighter jar-to-jar weight variation

improved product consistency and consumer satisfaction
A plan to improve Nesquik and Ovaltine production with real-time data
During production, Nesquik and Ovaltine undergo an agglomeration process that involves the wetting and drying of the product until it achieves optimal “fluffiness”—the right moisture and density.
At the Waverly factory in Iowa, operators ran the agglomeration process manually. Without a data-driven approach, there was sometimes unwanted variability in product moisture and density. This variability meant that while the product met the correct weight criteria, the container’s fill level was not consistent, and this needed to be rectified. So Nestlé designed a solution that uses real-time production data and advanced analytics to limit variability—consistently creating lower-density, fluffier chocolate powder.
Previously, the production line at Nestlé’s factory relied on manual samples to test powder moisture and density every 30 to 60 minutes. This manual process left operators with lagging indicators throughout each production run, which ultimately led to a lack of powder consistency. It also led to wasted product, since Nestlé would have to put more product in the jar to get it to a visually satisfying fill level. The question became: How can Nestlé get lower-density, fluffier powder that fills the correct volume in the jar?
“We wanted to have real-time predictions of the density and moisture of our product. We also wanted to give our operators manipulated variable suggestions, so they can make that more consistent powder on their own.”
—Greg O’Brien, Project Engineer and Project Owner, Nestlé
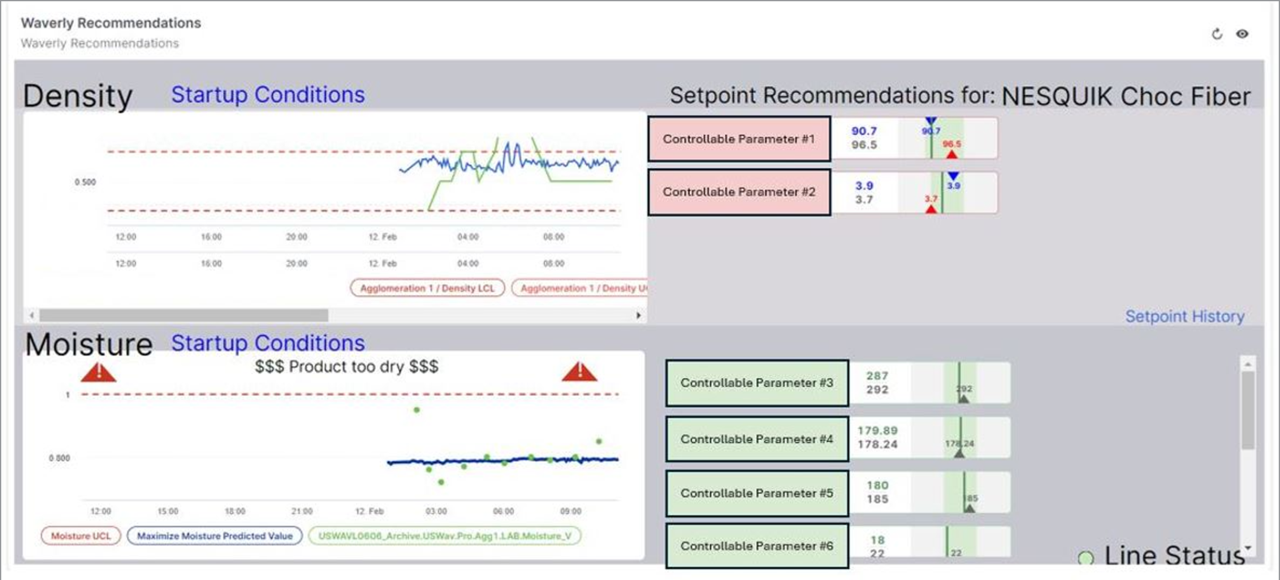
Cloud-based sharing enables powder data analysis
Nestlé’s teams wanted to use real-time production data to predict the powder’s moisture and density levels and generate setpoint recommendations to keep these levels within the desired limits. To do this, they first needed to get their production data in the cloud, where they could perform advanced analytics with AI and machine learning. The team transferred the necessary process data from one of the Waverly factory agglomeration towers into CONNECT data services, via AVEVA™ Historian. Within CONNECT, Nestlé rapidly developed a dashboard for operators to visualize predicted moisture, predicted density, and process setpoint recommendations¾all powered by AVEVA™ Advanced Analytics within CONNECT.
Operators can view customized dashboards, positioned next to SCADA screens, that show predictions and actual levels of density and moisture. Additionally, the solution’s setpoint recommendations panel takes the guesswork out of process control. Operators can simply follow the guidance AVEVA Advanced Analytics provides to ensure product consistency.
Solution
Deployed CONNECT data services, via AVEVA Historian, and AVEVA Advanced Analytics to predict quality parameters of powder production and recommend optimal process setpoints, removing the need for resource-constrained on-premises systems to carry the additional burden of supporting this solution.
Higher overall yield and less powder wasted
The Nestlé lighthouse team trained the no-code analytics models using historical process and lab data, establishing a correlation between the product’s quality parameters (density and moisture) and process variables. These models automatically generate setpoint advice for operators to use in the plant when making equipment adjustments.
The results were significant. During the lighthouse project’s one-shift eight-hour trial, the team saw more consistent powder produced with optimal moisture and density levels. At the end of the trial, the socks used to catch waste were mostly empty, with significantly reduced circulation of fine powder, which means less powder was wasted. Nestlé uses inline check weighers underneath conveyors to weigh every product as it passes along the line. The team found that the powder from the trial had consistently higher moisture and lower density, removing the need to overfill jars to reach the desired fill level. At the end of the trial, for every ten 1kg jars produced, Nestlé saved a 1kg jar of product—a 10% savings using the AVEVA solutions.
“Working with AVEVA’s lighthouse team helped us to understand how we can realize even more value from our solution in the future. For instance, running the solution in the cloud means we can easily roll out the analytical model to other plants across different regions without needing to invest in additional on-premises infrastructure.”
— Greg O’Brien, Project Engineer and Project Owner, Nestlé
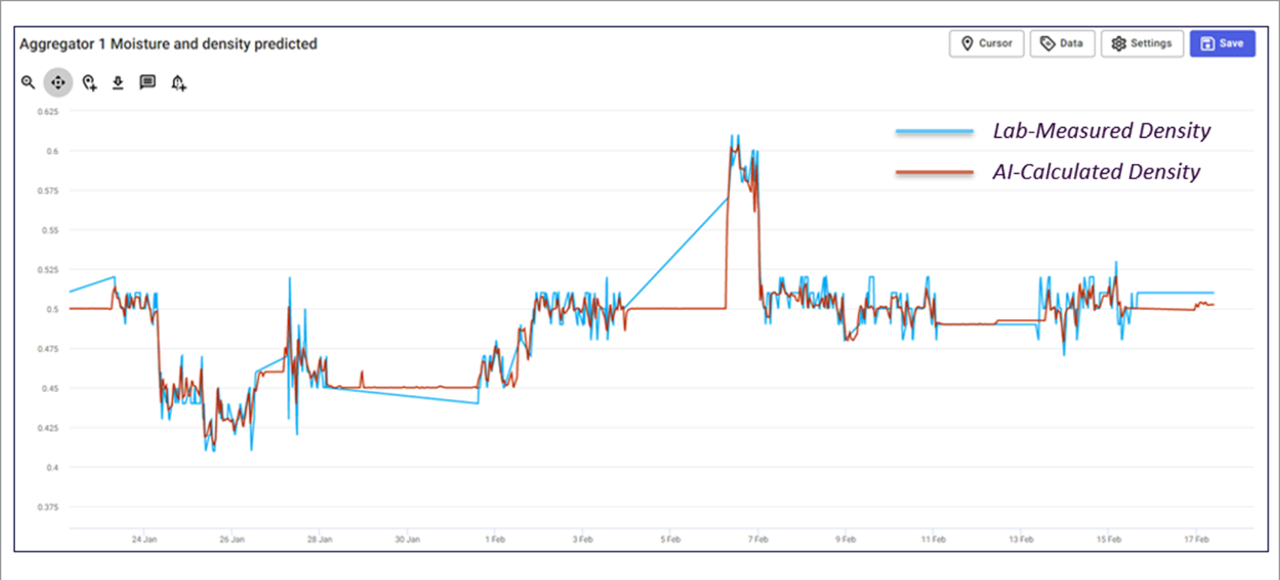
Cloud-based analytics delivered further value
Nestlé had a positive view of the models being run in CONNECT’s cloud environment, as it meant that their resource-constrained on-premises systems wouldn’t carry the additional burden of supporting the advanced analysis operations. Another advantage of running the solution on CONNECT is the ability to scale rapidly and flexibly. As Greg O’Brien states, “running the solution in the cloud means we can easily roll out the analytical model to other plants across different regions without needing to invest in additional on-premises infrastructure.” This not only accelerates the deployment process but also ensures that updates and improvements can be distributed globally with minimal effort. Nestlé can implement new features, conduct A/B testing, and deploy updates much more quickly in the cloud, helping the business continuously improve its processes and stay ahead of the competition.
Implementing the approach with other products
With the success of the lighthouse trial, the team is planning to adopt this approach across additional Nestlé products made with similar agglomeration processes, such as Carnation Breakfast Essentials and Malted Milk. While in the trial, operators had to make manual adjustments to the equipment based on the setpoint recommendations made by the model. The team expects to “close the loop” in the future, where AVEVA Advanced Analytics setpoint recommendations feed directly into Nestle’s SCADA for automated process adjustments. Looking ahead, the team also intends to use this methodology to optimize the consistency of pizza crust production.
Product highlights
Our industrial cloud platform: securely access the broadest and deepest industrial software-as-a-service (SaaS) portfolio enhanced by the power of industrial Artificial Intelligence (AI).
Maximize production efficiency, improve quality, energy efficiency, and throughput with cloud-based predictive and prescriptive insights.
Empower people with high-fidelity historical data from operations, enabling them to solve problems faster, make better data-based decisions, and increase productivity.