New Belgium Brewing Co. produce some of the world’s most popular craft beers. To ensure its beer-loving fans receive the highest quality beverages, New Belgium implemented a series of manufacturing automation initiatives to streamline and improve its brewing and bottling facility in northern Colorado. The company gained real-time insight into downtime events and drove process improvements with AVEVA solutions, increasing efficiency and production, increasing OEE from 45% to 65% in two years.
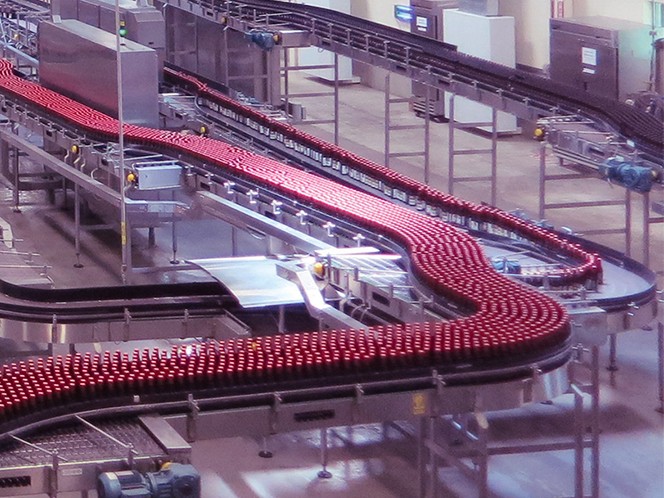
Challenges
The brewery lacked real-time information on unscheduled downtimes at various equipment areas which caused production slowdowns
Management needed to address gaps in methods and processes to drive improvements
With multiple facilities at different stages of digital transformation, New Belgium needed to ensure that beer from one facility was indistinguishable from beer produced at the next
Results
65%
OEE increased from 45% in just over two years
>50%
Decrease in downtime
25% - 30%
Increase in efficiency of scheduled run time

Achieved record production weeks producing 190,000 to 200,000 cases consistently
1.3M
barrels capacity per year in extended packaging area
100%
flavor-matched beers produced by all breweries
Streamlining bottling lines
Fort Collins, Colorado, USA − What started out as a beer-brewing hobby fueled by a passion for great-tasting craft brews has turned into one of America’s best multi-million-dollar success stories. Today, the folks at New Belgium Brewing Co. produce some of the world’s most popular craft beers, including Fat Tire and a multitude of other popular IPA, Pilsner, wheat beers and ales. To ensure its discerning beer-loving fans receive only the highest quality beverage, New Belgium implemented a series of manufacturing automation initiatives to streamline and improve its brewing and bottling facility in northern Colorado.
“New Belgium’s brewing operations were rapidly reaching capacity, and we needed to identify both efficiencies and inefficiencies in our bottling lines so the brewery could maintain its operating schedule,” said Joe Herrick, Packaging Systems Manager at New Belgium Brewing.
With AVEVA Manufacturing Execution System, AVEVA Operations Control, and the technical assistance of Apex Manufacturing Solutions and InSource Solutions, New Belgium achieved record levels of efficiencies in scheduled and non-scheduled downtime throughout its operations.
"The Apex solution is unique in the sense that it incorporates the same ‘ingredients’ that New Belgium utilizes for making great craft beer—creativity, knowledge, and experience.”
—Sam Vail, Chief Strategy Officer, Apex
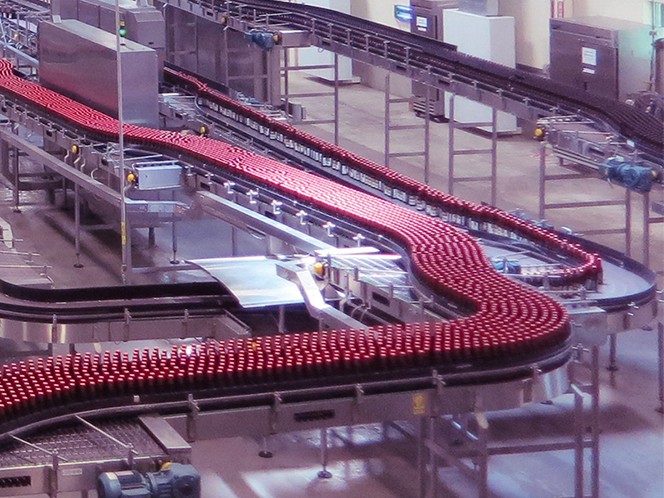
Finding time to bottle amid rising customer demand
When New Belgium’s operations management team took a closer look at its bottling line and measurement of cases produced based on the equipment’s capability, they realized its existing lines were capable of producing 294,000 cases a week, but in reality were only producing 150,000 cases each week.
An audit of its production line revealed that New Belgium was losing valuable packaging time during both scheduled and unscheduled downtimes. Its longtime manual data recording process, which involved managing paper production logs and spreadsheets, was just not enough to keep up with the level of bottling production New Belgium needed to achieve. “That’s when we realized it was time to rectify this situation,” Herrick said. The team enlisted the help of Apex Manufacturing Solutions to implement a new automation strategy to increase operational efficiencies, quality, compliance and overall performance.
With the implementation of AVEVA Manufacturing Execution System, Apex enabled New Belgium to use the data collected by the MES software to increase overall equipment effectiveness (OEE).
"AVEVA’s MES, coupled with New Belgium’s continuous improvement strategy, has increased our packaging line efficiency by 30%, saving us more than $400,000 annually in previously planned labor expenditures. It also has extended our packaging area capacity to about 1.3 million barrels each year. At this point, our approach to higher volumes is ‘bring it on’.”
—Joe Herrick, Packaging Systems Manager, New Belgium Brewing
Solution
Gained real-time insight into downtime events and invested in process improvements with AVEVA solutions, increasing efficiency and production.
Improved visibility brings increased production capacity
The brewery’s existing systems provided huge amounts of data, but without context. AVEVA Manufacturing Execution System provided a way to effectively collect and analyze that data in order to turn it into actionable information. Now, with greater visibility and a true understanding of actual production capacity for predictable order fulfillment, New Belgium can maintain its production and sales targets. Management is also able to effectively reduce production costs and improve overall product quality at the same time.
“At one point our filler was experiencing a significant amount of micro stops due to some bottles coming down the line that were falling down, or getting hung up on rails,” Herrick said. “The AVEVA software was able to provide us specific information related to these downtimes, so we had our team complete a Kaizan evaluation to figure out what we needed to do to improve it. We decreased our downtime by more than 50%. This is very significant for our business.”
By identifying the sources and the quantity of scheduled downtime as well as unscheduled downtime events, New Belgium could accurately track, record and address bottling performance. The operators can also maintain accurate packaging production schedules, and effectively manage the supply chain of materials needed during the packaging process such as bottle and can sizes and labels coinciding with each type of brew, as well as specific order requirements.
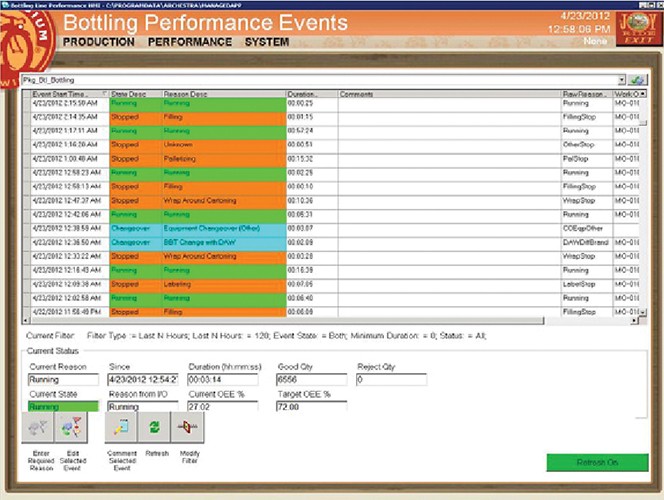
With enhanced visibility and real-time insights, the brewery saw that it needed to increase its maintenance staff to quickly address equipment repair issues. Increasing the maintenance team by 60%, adding a process improvement and analysis team, educating key staff in Kaizen processes, and training others in Six Sigma has allowed the company to react quickly to gaps in production methods, driving overall process improvements.
Achieving continuous process improvement through flexibility and scalability
The flexibility and scalability of the AVEVA’s MES software has enabled New Belgium to customize its product packaging systems to meet its unique requirements for the efficient flow of captured production management data from the plant floor systems.
The combination of AVEVA Manufacturing Execution System with the brewery’s existing installations of AVEVA InTouch HMI and AVEVA System Platform provides New Belgium the opportunity to ramp up automation processes as necessary.
“The model-driven approach of AVEVA System Platform gives us the ultimate platform for expansion when the customer wants to extend their MES system up, down, or sideways,” said Sam Vail, chief strategy officer at Apex Manufacturing Solutions. “With this unique scalability, we can start small without having to worry about switching to a different technology when the solution heads into uncharted territory.”
The AVEVA software solution at New Belgium Brewing can now quickly and easily replicate these automation processes at other areas of the company with its reusable engineering application. Reusable engineering objects and graphics allow Apex to provide a scalable solution that’s economical in scale for the customer as new areas of the plant are introduced into the reporting and graphics infrastructure concerning performance.
“The ability to customize graphics provided by the MES enabled Apex to develop a system that could effectively communicate the line status and production capacities in the New Belgium bottling and packaging lines, while at the same time illustrate the company’s unique company culture with engaging graphics,” Vail said. “Screen data shows what order is being worked on, what is coming next, and how the current rate compares to their standard.
“The advantages of using AVEVA’s MES at New Belgium Brewing in terms of operations is that we already have a mature InTouch HMI and System Platform environment, so implementation and integration are simplified. From an end-user point of view, we can combine functionality at the InTouch HMI, keeping their experience simplified and enriched with better information to operate their processes.”
—Lora Heckman, Business Applications Manager New Belgium Brewing
Multiple sites, same impeccable flavors
Since the completion of its first automation project with AVEVA, New Belgium has continued to explore AVEVA’s portfolio of operational solutions. More recently, New Belgium acquired two new brewing sites, formerly operated by competitors. Each new site, as well as the company’s other existing sites, are all at different stages in their automation journeys. That leads to an obvious challenge. How do you produce 100% flavor-matched beer across these different sites? “Especially with an acquisition,” says Frank LaBarbera, Automation Engineer at New Belgium Brewing, “you get handed low documentation; you get handed a facility with different capabilities, but there’s the expectation of making beer that is completely indistinguishable from beer made at all the other facilities.”
Working with AVEVA Select Partner InSource Solutions, New Belgium found its solution in AVEVA Operations Control. The solution allows the team at New Belgium to first pilot new operational strategies at sites that are more advanced in their automation journeys, like the company’s Ashville site. Once successfully implemented at a more mature site, New Belgium can adjust the automation strategy and propagate it to its other breweries—rapidly. “On a Monday,” says LaBarbera, “we figured out what we needed to do to show all our air monitoring data.” This includes CO2, sulfuric acid, and other measurable factors in air quality. “And by Thursday, we had it implemented at all the other sites.”
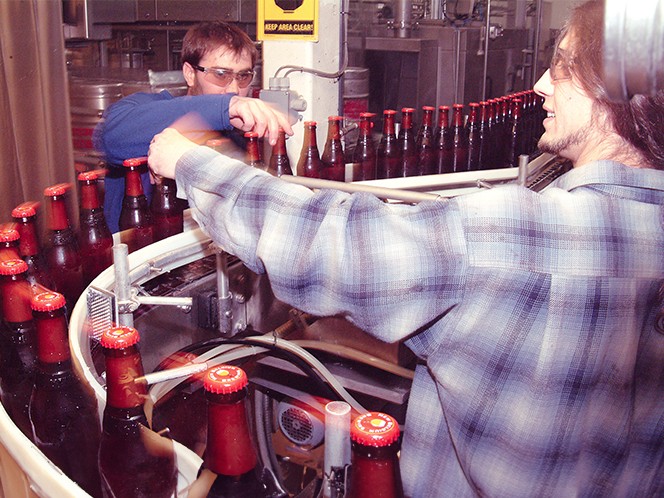
Rather than needing to have the perfect strategy devised at the outset—before the team is even familiar with the technology—AVEVA Operations Control gives New Belgium the architectural and licensing flexibility to learn what it needs as it progresses. “AVEVA Operations Control lets you figure out what you want from the technology in a more evolving, dynamic way,” says LaBarbera.
Tapping the future
In brewing, and in the food and beverage industry as a whole, mergers and acquisitions have been and will continue to be a common fact of life. Thankfully, with the help of advanced digital solutions, big changes don’t have to be big challenges. “When you get a brand new place that had a different mindset, and had different licensing requirements, and different software, and maybe completely different hardware,” says Frank LaBarbera, “you get to make many, many more flexible judgement calls.”
New Belgium Brewing’s digital transformation has given it the flexibility and adaptability it needs to maintain a tradition of excellence even in an ever-changing business environment. “You get to actually get things done in a very reasonable time frame,” says LaBarbera, “and with minimal effort.”
Product highlights
Maximize profitability, flexibility, quality, and compliance in manufacturing by digitally managing the rules and information for all operational activities and plant events in real-time. A work process-centric and Model-driven approach reduce the time to value and cost of ownership for both plant deployments and multi-site MES rollouts.
Contextualize operations with responsive, standards-driven, and scalable software for deploying advanced SCADA, MES, and IIoT. Unify people, processes, and assets.
The productivity software necessary to run any modern real-time operations. It combines process visualization, collaboration and digital knowledge sharing, advanced analytics, operational shift and regulatory reporting, and AI/ML into a comprehensive, unlimited operations software.
AVEVA InTouch HMI is HMI visualization software for operators to achieve real-time operations visibility. The world’s most widely used plant HMI for process monitoring and control.