SCG Chemicals has one of the largest petrochemical supply chains in all of Asia. To keep it running efficiently, asset reliability is paramount. Asset failures can quickly lead to supply chain interruption, which cost the company substantially. That’s why SCG Chemicals relied on a suite of AVEVA solutions to build a digital twin of plant operations. Its new Digital Reliability Platform increased asset reliability to nearly 100% and ensures reliable operations across the supply chain at all times.
Challenges
Greater real-time visibility of plant performance needed
Building a digital operating system to make its zero-unplanned-downtime vision a reality
Visualizing data, tracking KPIs, and accessing analytics-based decision support
Results
99%
plant reliability attained
9x ROI
achieved in six months

end-to-end visibility of plant operations

operational digital twin supports decision-making

real-time data and analytics to predict equipment health

data visualization promotes an understanding of plant performance
Building a platform for asset reliability
With such a tightly integrated business, an individual equipment failure could shut down SCG Chemical’s entire production chain with direct implications for top and bottom-line financial performance. To address this risk, SCG Chemicals built a data-driven advanced asset performance management (APM) solution to monitor critical assets and predict failure towards a goal of zero plant shutdowns.
The company partnered with AVEVA to develop a Digital Reliability Platform (DRP), a complete asset performance management solution that predicts equipment health, monitors performance, and enables advanced maintenance to eliminate unplanned downtime. Using a mix of on-premises and cloud-based applications, the solution integrates online and offline equipment data to visualize plant performance. The platform also applies artificial intelligence (AI) for predictive maintenance and issue resolutions.
During a five-month pilot project, enabled by the AVEVA™ Flex subscription program, SCG Chemicals validated the Digital Reliability Platform and commissioned its Digital Reliability Center, the company’s central hub for data collection, analysis, visualization, and maintenance operations. With the success of the DRP, SCG Chemicals is scaling up the platform to its 15 plants as well as its joint ventures.
Platform requirements for asset reliability
When evaluating technology partners for its APM strategy, SCG Chemicals focused on three factors:
- End-to-end solution – the ability to deliver a complete APM solution to integrate and analyze data, visualize performance, and manage maintenance activity.
- Workforce enhancement – tools for teams to access data quickly and guide actions to perform maintenance tasks using enhanced information via tablet, video wall, and mobile operator rounds.
- Strategic partnership – a technology provider with deployment expertise and deep knowledge of process manufacturing, with a subscription program that gives full flexibility to access a solution ecosystem.
Importantly, in its efforts to reduce unplanned downtime, SCG is also driving business transformation to improve the knowledge and behavior of its workforce.
Solution
The Digital Reliability Center, a plant digital twin that integrates real-time visibility of operations and predictive analytics
AI-infused predictive analytics and virtual plant
The Digital Reliability Platform provides SCG with an enhanced ability to maintain equipment in various plants within its business, both in Thailand and abroad. The central components of the Digital Reliability Platform include:
- Predictive analytics – AVEVA™ Predictive Analytics monitors equipment behavior continuously in real time and alerts operators when current operation deviates from historical trends. The solution applies data science principles to manage large datasets to detect machine abnormalities. In addition, a rule-based engine monitors equipment health by incorporating online and offline data from different sources and helps determine the remaining useful life (RUL) of the equipment.
- Data center – The DRP gathers offline and online data into a centralized data management platform, which serves as an operational data repository and a base for rules configuration. The data center collects real-time, time series data and then contextualizes it and feeds it into predictive analytics.
- Advanced maintenance – AVEVA asset performance management tools enable advanced maintenance with features such as offline data entry including work requests; work order closure via mobility; and work order scheduling connected through SAP Solution Overview.
- Operational digital twin – The DRP features a digital twin, a virtual 3D plant model with complete machine information represented within the model. The digital twin provides an immersive environment that allows interdisciplinary collaboration and fast access to plant information through AVEVA™ Asset Information Management and dashboards for equipment status, alarms, and health status. Management uses this digital twin to plan work efficiently and respond to emergency events if they arise.
“The Digital Reliability Platform is an unprecedented step forward to ensure reliability for our business. AVEVA was the only company able to provide an end-to-end solution spanning engineering, operations, and maintenance. With the DRP, we have successfully brought together big data, AI, machine learning, and predictive analytics into a practical solution that will empower our workers and improve our performance. This is a great achievement and innovation for SCG Chemicals.”
–Mongkol Hengrojanasophon, Vice President, Olefins Business and Operations, SCG Chemicals
Plant reliability increased from 98% to nearly 100%
Since implementing AVEVA software, SCG has seen considerable business value:
- Plant reliability – plant reliability has increased from 98% to nearly 100% through catch identification to avoid asset failures. The savings from avoided asset failures amount to nine times SCG’s return on investment.
- Reduced maintenance costs – SCG reduced maintenance costs by 40% through greater operational and workforce efficiency, as well as improved work scheduling.
- Asset strategy optimization and remediation – Optimized planned maintenance through the use of data from IIoT sensors and real-time analytics, reducing costs by up to 30%.
- Access to actionable information – the time to retrieve actionable information has been reduced to less than 10 seconds, through the centralized data platform and automated reporting.
- Scalable software usage – the central license management portal allows SCG to scale its software use based on its needs, either by allocating credits across teams and sites or adding new credits to its existing AVEVA Flex contract.
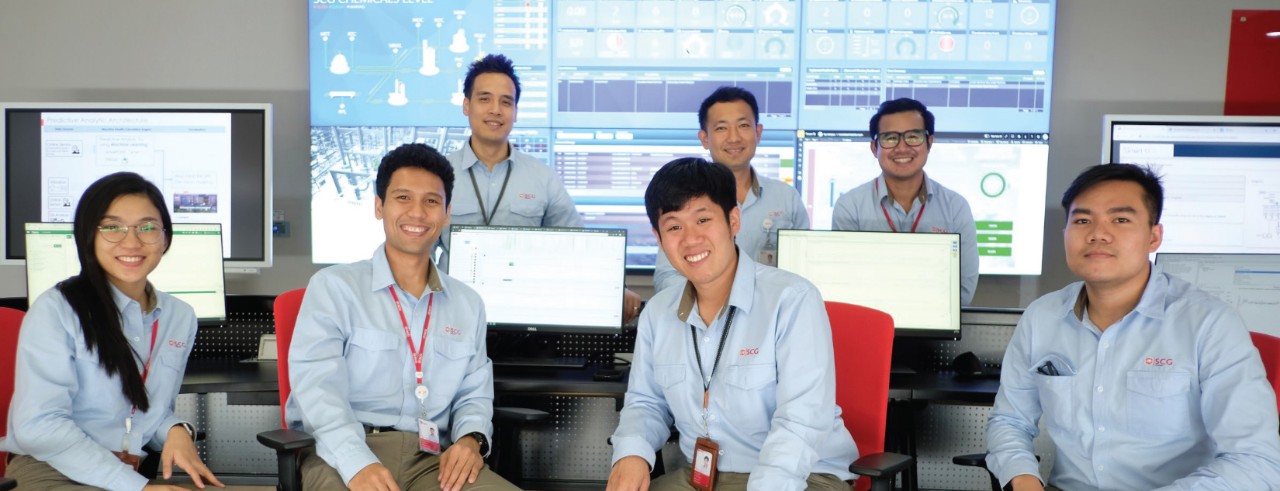
A new era for asset reliability
With a range of dashboards from the business unit level down to individual equipment, the Digital Reliability Center changes how SCG teams interact with their data by providing a single interface for all asset information. AI and machine learning technology help teams analyze equipment status and provide prescriptive recommendations and actions. The faster teams can access information and correlate it with real-time data, the faster they can resolve and identify errors that occur. The result is an increase in operational efficiency as well as early detection of abnormalities to prevent equipment damage or failure.
The Digital Reliability Center is the latest advance by SCG Chemicals to drive industry innovation and leadership. With its digital innovations to increase work efficiency and safety, SCG Chemicals is establishing a new competitive standard within the industry.
Product highlights
Use data from multiple sources to visualize, validate, and collaborate on digital twin data.
Reduce unplanned downtime and maximize asset reliability with AI-infused predictive maintenance for early warning and diagnosis of equipment issues.
Unlock new capabilities with the intelligence platform that brings together your unique industrial ecosystem.
Learn more
Connect people, systems, and data that empowers them to make data-driven decisions that boost profitability, reliability, and safety.
Learn more