TotalEnergies is diversifying its energy production to include renewables and moving toward net-zero emissions. To achieve this goal, it needed to precisely measure its current emissions. It used AVEVA™ PI System™ to collect data across all its operations and made this new pool of data available to its teams. The company has also begun monitoring downstream activities remotely and used advanced analytics to anticipate equipment failures, saving €1.5M and 64 days of downtime in just one year.
Challenges
Different teams using different calculations and visualizations of data
Tracking and mitigating greenhouse gas emissions using a cost-effective scalable digital solution
New energy sources require new approaches to monitoring and maintenance
Results

a sustainable digital twin with models, analytics and enterprise visualization

models and templates built once and then applied to hundreds of equipment and assets

real-time data calculations, analysis and KPIs
15%
reduced CO2 emissions annually in one use case
500,000
barrels saved by avoiding an upstream production shortfall

avoided catastrophic equipment failure
Using real-time operational data to reduce greenhouse gas emissions
TotalEnergies implemented more than 110 greenhouse gas emissions reduction projects in one of its initiatives for cleaner energy production. These projects focused on monitoring energy efficiency by equipment as well as greenhouse gas emissions by source. A longtime user of AVEVA products, the company wanted to leverage the tools it already had. So it started building monitoring models using its suite of AVEVA solutions.
The company fed data from various on-site rotating and firing equipment to headquarters in France using AVEVA PI System. After verifying and contextualizing the data using AVEVA PI System’s data archive and asset framework, the team then conducted analysis based on real-time information about flows, temperatures, power, and pressures, alongside equipment data sheets and gas composition data. AVEVA™ PI Vision™ and Power BI then displayed all the critical information in dashboards that allowed users to see an overview of total emissions of a site or drill down into specific equipment and KPIs.
The company used this data to calculate emissions per equipment as well as the specific energy efficiency for each asset. In all, it has monitored about 85% of emissions from operations. And now that these models are built, TotalEnergies can apply them to hundreds of other equipment and processes. The models provide real-time data calculations, analysis and KPIs to help the team identify and prioritize emissions reduction opportunities. In one use case, in which the company set out to optimize power delivery configuration of a site, it reduced CO2 emissions by 15% annually.
“Most of our sites are using [AVEVA] PI System, so most of the data is already available, but not really used properly to monitor the emissions, and this is why we decided to use [the asset framework function of AVEVA PI System] to design the proper templates to help them to monitor efficiently the emissions. Now the information is available to the operations people.”
—Pierre Bernadi, Technical Advisor, TotalEnergies
Reducing critical equipment failures and operating more efficiently
In addition to the monitoring of greenhouse gas emissions, TotalEnergies wanted to reduce unplanned equipment downtime to drive more efficient operations. A few years ago, the company saw an increase in mechanical failures in critical equipment for purposes such as power generation, water injection, and gas compression in its growing fleet. Among the 105 breakdowns recorded, it discovered that half of them could have been avoided with proper remote monitoring and early warning detection. In 2019, an accident caused production to be halted for six months, which resulted in a loss of 120,000 barrels a day and several tens of millions of dollars (USD) in costs.
To mitigate and prevent such losses, the company implemented its Remote Assistance Intervention and Diagnosis (RAID) system. The system gathered data from equipment sensors fed to AVEVA™ PI Server, then fed that data to headquarters to run more advanced analytics using AVEVA™ Predictive Analytics. There was no additional cost to get data from the sensors, as this data and its storage was already in place. AVEVA Predictive Analytics and AVEVA PI System seamlessly work together to allow users to generate more insights. Users can cleanse AVEVA PI System data, develop no-code, AI-driven predictive models, and use prescriptive guidance in analyzing results to identify potential asset failures before they occur.
TotalEnergies deployed RAID upstream on 320 shaft lines, delivering a total of 36,000 alerts, with 429 critical equipment catches. Downstream, teams acted on 210 critical alerts. They avoided a production shortfall in upstream production, almost 500,000 barrels saved. Also, TotalEnergies avoided a catastrophic equipment failure like the one that happened in 2019.
Beyond these quantitative gains, the company has optimized maintenance and enhanced asset management. It has fostered internal capabilities to build other monitoring tools, such as online gas turbine carbon emissions monitoring, centralized centrifugal compressor performance monitoring, and a power reserve monitoring tool. TotalEnergies plans on focusing on wind next, adapting upstream activities and knowledge to this new industry. It has already deployed a remote monitoring system for one turbine in Scotland, with plans for mass deployment to a full wind farm soon.
Solutions
A robust data contextualization and governance platform to break down business silos, increase maintenance efficiency, track emissions and find new operational solutions
Early warnings of equipment failures and implement a predictive maintenance strategy to avoid unplanned downtime
Verified and standardized data down to the molecular level, with reliably tracked CO2 and SO2 refinery emissions
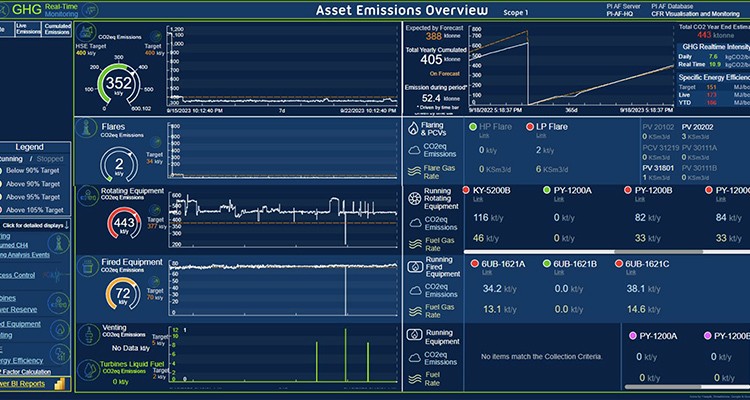
Users can see an overview of total emissions of a site, or drill down into all specific equipment and KPIs
Down to the molecule: Standardizing refinery data
One of the challenges TotalEnergies experienced on the road to more sustainable operations was the numerous teams involved in energy and emissions monitoring. These teams were using the same source information, but there wasn’t a standardized approach to accessing, analyzing, and acting on the information. Calculations performed by different teams were often duplicated and not always shared, leading to inconsistencies. So the company created a new branch, OneTech, consisting of 3,400 engineers, researchers, technicians, and support, to centralize its technical expertise to serve all operational branches.
Using the asset framework function of AVEVA PI System, the team set out to add deeper structure and standardization to all asset data. The molecule is the primary source of information in this process of standardization. The team starts with the energy content of the molecule, along with the carbon dioxide and sulfur dioxide produced by combustion. They create a master template with the intrinsic properties of the molecule that can be applied to any number of different use cases. Rolling up the data all the way to the refinery level, the team can compare calculated emissions with what is measured by their online analyzer instantaneously or from daily, monthly, or yearly values. This information is then visualized in AVEVA PI Vision, so users can see exactly which piece of equipment is experiencing an issue or at which stage in the process a problem occurred and can act.
Emissions and energy monitoring are now based on the same information. Templates are generic and fully scalable. The team already deployed this system at four refineries, with more than 45 pieces of combustion equipment. Now, these templates can be applied to endless other use cases—and not just monitoring use cases, but optimization use cases too. Having validated the calculations in the creation of the master templates—beginning with verified molecular calculations—the team has paved the way for application across the enterprise. These templates can also be re-used for other purposes, such as CO2 consolidation at the process unit level.
“Now that we've established all the monitoring tools, let's proactively identify opportunities to reduce greenhouse gas emissions.”
—Juan Guzmán, Digital Lead, TotalEnergies
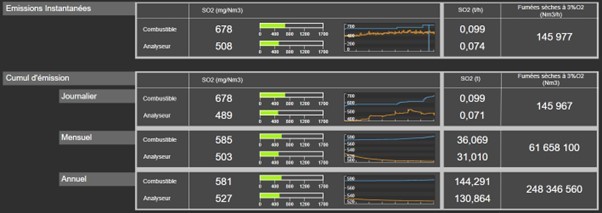
The energy use and emissions of each combustible can be calculated using master templates based on the makeup of molecules
Start small, think big: Data governance and synergy across use cases
TotalEnergies realized that a strong central data governance strategy not only ensures operational efficiency and optimized energy use today, but will set the company up for future innovation and success. It has created a robust data contextualization platform using AVEVA PI System, particularly with the asset framework function, along with AVEVA PI Vision, to break down business silos, increase maintenance efficiency, help track emissions and find new solutions. As oil and gas companies endeavor to adapt to and even lead the energy transition, TotalEnergies becomes a beacon of what that can look like.
Product highlights
Collect, aggregate, and enrich real-time operations data for immediate problem-solving and easily deliver formatted data to enterprise applications and advanced analytics.
Reduce unplanned downtime and maximize asset reliability with AI-infused predictive maintenance for early warning and diagnosis of equipment issues.
A self-service dashboarding tool for context-driven display, on-the-fly analysis, and secure sharing of your AVEVA PI System data—accessible anywhere on any device.
Related success stories
Stay in the know: Keep up to date on the latest happenings around the industry.