Vivix, a leading float glass plant and the only fully Brazilian one, opened its first factory in 2014 with advanced automation and technology. However, it lacked an as-built design and relied on an external company for engineering data. To enhance its capabilities, Vivix used AVEVA products to digitize a 3D model of the plant, integrating it with its systems and storing it in the cloud. By 2021, Vivix used this digital model to efficiently design a second plant, improving efficiency, cost-effectiveness, and sustainability.
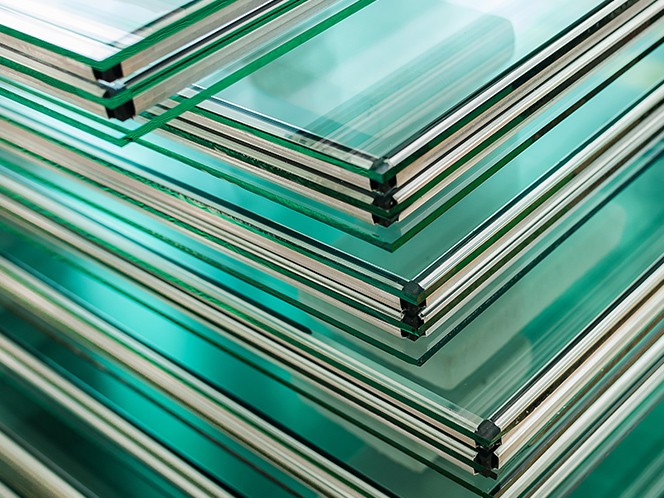
Challenges
Not owning engineering data
Updating data was costly, laborious and error-prone
Struggled to store and share engineering data
Results
15%
reduction in engineering project costs
50%
reduction in travel expensesr
80%
reduction in reliance on IT team

reduced engineering CAPEX by making local servers unnecessary
When Vivix Glass opened its first factory in 2014, this first plant had a cutting-edge design, high levels of automation and top-notch technology, such as a low-energy melter. But the engineering aspects of the plant did not match the high standards of its operations technology. Vivix never had an as-built design of the plant, none of the documentation was 3D and it depended on an outside engineering company to keep track of its engineering data, including records of post-construction improvements.
To bring its engineering capabilities up to par with its operations, Vivix used AVEVA products to digitize a 3D model of the entire plant. It connected that model to its document and maintenance systems, took ownership of all this data and made it available online in the cloud. When it came time to start designing a second float glass plant in 2021, Vivix had 3D catalogs and specifications in hand that made engineering more efficient, affordable and sustainable.
"Today we are in a completely different scenario, planning and executing our expansion project with collaborative, cloud-based tools that allow greater technical and budgetary efficiency."
--Claudia Lima, Engineering manager, Vivix
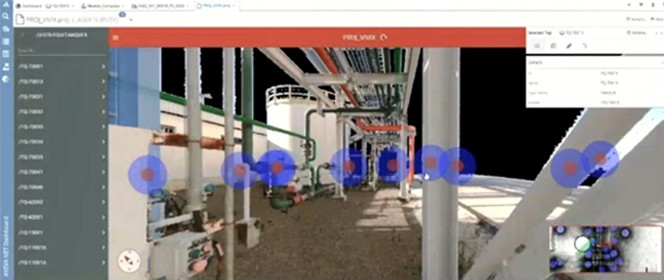
Building a 3D model
Vivix’s first plant came online in 2014 without an as-built design, 3D databases, or a good catalog to manage and control its material. It only had 2D documentation, such as drawings, isometrics and diagrams. Vivix also didn’t control its own databases in which to register the improvements it made to the plant over the five years after construction.
So, in 2019, its engineering team started a digital twin project. It hired an engineering company to laser scan the entire plant and used AVEVA™ E3D Design to build a 3D model over that scan. It shared both the laser scan and 3D model over web browsers with AVEVA™ Point Cloud Manager so stakeholders could check the progress of the project online.
The engineering team used AVEVA™ Asset Information Management to connect elements of the 3D model to Vivix’s document and maintenance systems. Building the 3D model and connecting it to Vivix’s other systems only took about 12-18 months. What’s more, this project also gave Vivix 3D catalogs and specifications that it used to start designing its next plant, starting in 2021.
Solution
Vivix uses AVEVA E3D Design, AVEVA Point Cloud Manager, AVEVA Asset Information Management and AVEVA™ Unified Engineering to construct and augment a 3D model of its plant with information on instrumentation, maintenance, material and other subjects. It owns all this data so it can access and share it with its engineering partners in the cloud via CONNECT.
Sharing data in the cloud
Vivix finally had all the engineering data it could want on its plant: 4.4TB that updated every month. But, managing all this data posed new problems.
At first, it used external hard drives and courier services to transfer data across the country between its plant and its engineering partner. Besides being time-consuming, this method posed obvious security concerns. It also required Vivix workers to travel across country to meet with the engineering company to verify the quality of its deliverables.
To make transferring data more secure and efficient—and give Vivix ownership over its own data—the company adopted a hybrid solution in which it stored much of its information in the cloud on AVEVA’s industrial intelligence platform, CONNECT, while still keeping some on premises with AVEVA Asset Information Management.
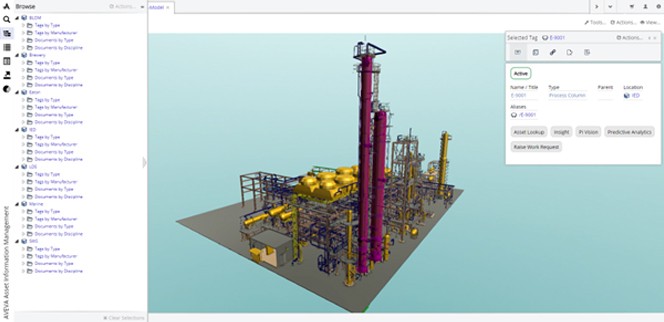
Vivix’s engineering partner already had its own cloud infrastructure, so Vivix used AVEVA Global to transfer data between its CONNECT databases and its engineering partner’s cloud system. AVEVA Global allows Vivix to determine which of its databases the engineering company can access, and whether it has read access, write access or both.
"The migration to the cloud with [CONNECT] combined with the use of AVEVA Global, allowed the initial phase of the project to be developed in a unified environment, with a unified catalog and shared database between the factory engineering and designer’s engineering"
--Claudia Lima, Engineering manager, Vivix
Greater engineering efficiency and lower CAPEX
Vivix’s engineering transformation has made its operations more efficient and sustainable. Because all its engineering databases are in the cloud on CONNECT, it no longer depends on local servers, which reduces its CAPEX. It has also reduced its dependence on its IT team by 80% and enjoys flexible OPEX based on how much it uses its software.
Now that it shares engineering data in the cloud, it no longer has to fly representatives back and forth to its engineering partner. As a result, its travel expenses are down 50%, which also cuts its carbon emissions.
Vivix’s use of the 3D catalog and automatic data sharing in the cloud cut 15% from its engineering project costs. On top of the cost reduction, it also gets real-time access to its information, so it catches and reduces inconsistencies.
Vivix’s engineering transformation gives it a cloud-based foundation that continues to give it operational agility as it plans to expand its manufacturing capacity to 1,900 tons/day and become the second largest Brazilian company in its sector.
Product highlights
The most advanced and powerful 3D design solution, enabling dash-free multi-discipline design to maximise engineering and design efficiency.
Our industrial cloud platform: securely access the broadest and deepest industrial software-as-a-service (SaaS) portfolio enhanced by the power of industrial Artificial Intelligence (AI).
AVEVA NET is a powerful web-based Information Management solution for engineering and operations. It brings together information from multiple sources and in multiple formats to enable users across your business to securely access, visualise, validate and collaborate on the Digital Asset data.
Capture the 3D baseline of your existing brownfield asset in a simple, accessible and secure workflow with AVEVA Point Cloud Manager.
AVEVA Unified Engineering provides end-to-end integration of conceptual, FEED and detailed design that handles all process simulation and engineering (1D, 2D and 3D) from one single data hub, providing greater agility and increased engineering efficiency.