Operational Safety Management
Plan and perform safe, compliant working on complex engineering assets. AVEVA Operational Safety Management enables asset operators to eliminate, minimize, or mitigate operational risk while optimizing asset performance.
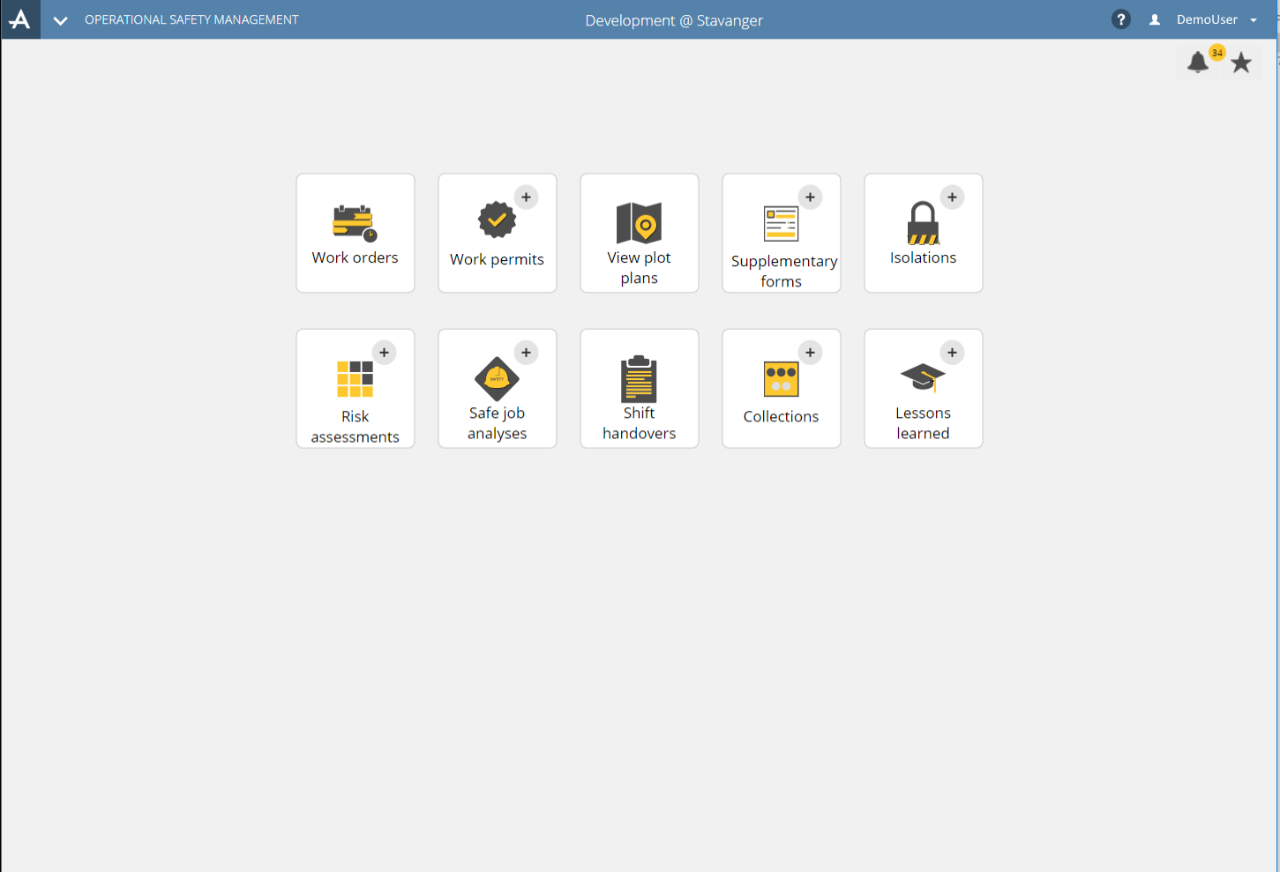
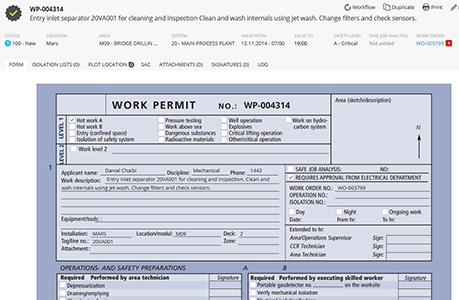
Reduced Risk
- Consistent, compliant, best-practice execution of invasive tasks eliminates, minimizes, or mitigates risks to personnel, to the asset, and to the environment.
- Enforced use of validated procedures minimizes the risks associated with shutdown and restart.
- Verification of sustained regulatory compliance avoids the risk of fines or loss of operating licenses.
Increased Standardisation
- Efficient, compliant, best-practice operation can be standardized easily across multiple assets.
- Staff can be redeployed between assets with a minimal learning curve.
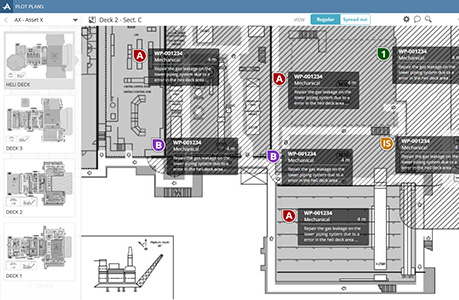
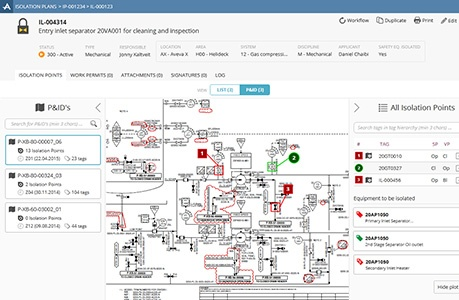
Reduced Operating Costs
- Efficient deployment and use of valuable skilled resources save direct labor costs.
- Efficient, rapid execution of engineering tasks minimizes loss of production.
- Robust control and audit trails reduce the costs of demonstrating regulatory compliance.
Features and Capabilities
Risk Assessment
A configurable, rule-driven framework guides the user in assessing every relevant risk and making the appropriate decisions.
Work Permit Management
A configurable, rule-driven framework manages the entire existence of each Work Permit, from its creation to closure and archiving.
Work Activity Plotting
Unique, best-in-class visualization features show the various work locations on the asset, enabling task clashes to be avoided and highlighting opportunities for coordinating tasks in close physical proximity.
Isolation Planning and Execution
Both mechanical and electrical isolations can be applied consistently, quickly, and in compliance with applicable regulations and best practices. Mechanical isolation plans can be efficiently created by direct visual interaction with intelligent P&IDs
Safe Job Analysis
Structured, template-based identification of risks, causes, and effects is complemented by controlled documentation of safety meetings and management of the approval process.
Lessons Learned Reporting
Continual improvement of operational processes to drive down risk and increase efficiency is supported by tools for capturing lessons learned on individual tasks and identifying common factors in their execution.
Discover latest news and resources
Check out the latest news, and success stories