AVEVA Process Optimization: Reactor Models for Refineries, Ammonia and Petrochemical Plants
Rigorous kinetic models integrated with Reactor Models provide optimization, LP update, performance monitoring, as well as offline simulation.
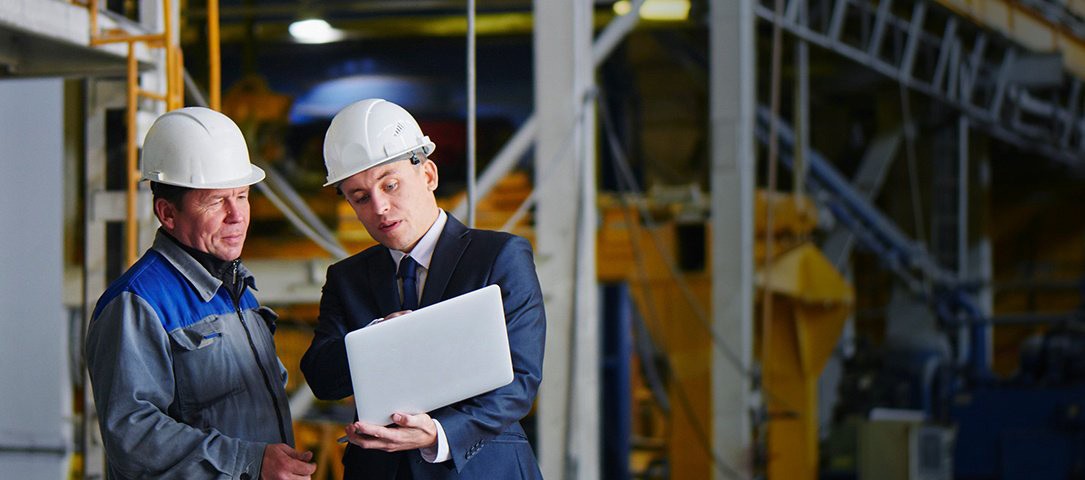
Rigorous kinetic models with mass and heat balance
Conversion units are usually your most complex units in a refinery or chemical plant due to their reaction nature. These units can be very nonlinear with behavior that is very difficult to predict. This poses a challenge in controlling and operating your units, let alone optimizing the operation. Our rigorous kinetics-based models, together with Process Optimization’s open equation-based platform, data-reconciliation, and auto-tuning functions, can always provide an up-to-date representation, or digital twin, of the conversion units. This opens-up a whole different world on what can be achieved with your reactor models.
Reactor Models
Our Reactor Models are the digital twin for operation of the reactor units in your refinery or petrochemical plant.
Real-time optimization (RTO)
Our reactor models enable Process Optimization to model, simulate and optimize a reactor unit, a train of several connecting units containing reactor units such ad an integrated Crude Distillation Unit-Resid hydrodesulfurization-Resid Fluid Catalytic Cracking (CDU-RHDS-RFCC) unit, or potentially a whole refinery. RTO on a Fluid Catalytic Cracking (FCC) unit can help you acheive $0.10 to $0.20/bbl of benefit. With an integrated RTO you can generate more benefit than the combined benefit of individual unit RTOs due to global optimisation of combined units. One example is a CDU-FCC integrated RTO, the optimisation requests the CDU to change the cuts to maximize the benefit of your FCC unit, an optimization move that an individual CDU optimization will not be able to see.
Linear Programming (LP) Update
Refinery planners are faced with the challenge of updating LP vectors to reflect the constantly changing feed and operating conditions of your refinery. Without up-to-date LP vectors, the planning model will not reflect the real plant and you may not capture full potential which could result in financial losses.
With rigorous reactor models tuned with plant and lab data, Process Optimization can generate yield data that can be transformed to LP vector format by the LP Update Manager. With an intuitive and easy-to-use interface, the LP Update Manager is designed to allow the process engineers and planners to construct a mapping from the Process Optimization variables to the LP vector variables with minimum effort and use the mapping to generate new LP vectors from plant data tuned, up-to-data reactor models. The LP Update Manager also trends historic LP vectors so planners can keep track of changes in LP vectors, due to condition change.
Performance monitoring
For a reactor unit, one key operating objective is to sustain the catalyst activity for longer turnaround time and reduced catalyst cost. Without a rigorous reactor model, it is difficult to measure the catalyst activity from plant data. With our reactor models, together with Process Optimization’s auto-tuning capabilities, the catalyst activity, along with product selectivities, properties and other reactor related KPIs, can be updated and monitored real-time. KPIs of other equipment in the unit, for instance, column efficiencies, heat exchanger filing, compressor efficiencies can also be updated and monitored. Your operation and maintenance team can use KPI trends to evaluate the performance of your operation, equipment and catalyst, and to make informative operation, maintenance and business decisions such as optimal operating condition to sustain catalyst activity, maintenance schedule, and catalyst selection and purchase.
Offline process engineering, simulation, offline optimization and case study
A rigorous reactor model tuned by reconciled current plant and lab measurement data provides your process engineers with the best insight of the reactor’s behavior. With up-to-date reactor models, process engineers can do process simulation, debottlenecking, what-if analysis and offline optimisation, with great confidence.
AVEVA Process Optimization: Reactor Model Portfolio
Refinery
- Fluid catalytic cracking (FCC) and resid fluid catalytic cracking (RFCC)
- Hydrocracker
- Hydrotreater
- Lube hydrotreater
- Resid hydrodesulfurization (RHDS)
- Catalytic reforming
- Hydrofluoric acid alkylation
- Sulfuric acid alkylation
- Delayed coker
- Visbreaker
- Light naphtha isomerization
Ammonia
- Primary and Secondary steam reformer
- High and low temperature water-gas shift
- Methanation
- Ammonia converter (radial, axial and cross flows)
Coal Gasification
- Coal Gasification (Slurry entrained gasifier)
- Water-gas shift
- Methanol synthesis