Manufacturing Execution System
What is a manufacturing execution system (MES)?
A manufacturing execution system (MES) is a software solution that plays a crucial role in controlling and optimizing operational activities and manufacturing processes. It serves as a bridge between the enterprise resource planning (ERP) system and the shop floor, providing real-time visibility into plant operations for both the factory and the supply chain.
One of the key purposes of MES software is to automate data collection and digitize manual procedures, eliminating the need for paperwork and reducing human error. It enables manufacturers to gain better control over their production processes and quickly take corrective actions when required, leading to improved quality, reduced downtime, and increased throughput.
By capturing all data related to the transformation of raw materials into finished goods, a MES provides the data foundation to continuously improve overall equipment effectiveness (OEE) and productivity.
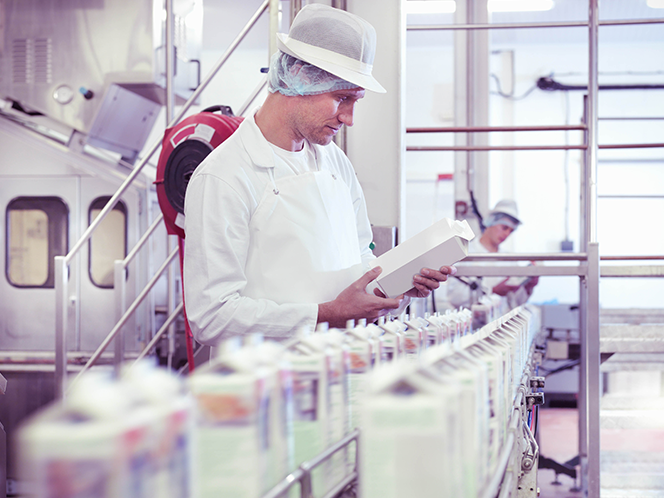
What does a MES do?
A MES enables manufacturers to achieve operational excellence by synchronizing all operational activities on the shop floor across inventory, production, quality, and maintenance operations, maximizing resource utilization, minimizing waste, and ensuring compliance with regulatory standards.
The key components and functionalities of a MES include:
- Production management: A MES captures and monitors all operational activities and automated production in real time. It captures data from various sources on the shop floor, such as machines, sensors, and operators. This data includes all production events and counts, cycle times, quality and asset utilization metrics, and more.
- Production scheduling and planning: A MES helps in creating optimized production schedules based on visibility into available resources and capacity. It ensures efficient allocation of machines and materials to deliver customer orders on time and in full.
- Inventory management: A MES keeps track of raw materials, work-in-progress (WIP), and finished goods inventory. It provides accurate inventory visibility, ensuring timely replenishment, and provides seamless product genealogy and material traceability within the four walls of the plant.
- Quality management: A MES facilitates quality control by enforcing standard operating procedures (SOPs) for conducting inspections, capturing quality data, and triggering corrective actions when deviations occur.
- Performance analytics and reporting: A MES generates comprehensive reports and analytics on key performance indicators (KPIs) to monitor production efficiency, identify bottlenecks, and drive continuous improvement.
What are the benefits of using a MES?
One of the key benefits of a MES is improved production efficiency and visibility. With real-time data collection and analysis, a MES enables manufacturers to identify bottlenecks, optimize workflows, and make informed decisions to enhance overall efficiency. By monitoring and analyzing production data, manufacturers can identify areas for improvement, reduce cycle times, minimize downtime, and ultimately increase production output.
Another important advantage of a MES is enhanced quality control and compliance. Manufacturers can ensure product quality and traceability by capturing and tracking critical data throughout the production process. A MES enables real-time monitoring and control of critical quality parameters, facilitating early detection and resolution of quality issues. Furthermore, a MES allows manufacturers to track materials, components, and processes throughout the entire production lifecycle, ensuring adherence to regulatory requirements and enabling effective product recalls, if necessary.
Streamlined scheduling and resource allocation is yet another benefit of a MES. With a MES, manufacturers can align production orders with available resources, minimizing idle time and maximizing equipment utilization. A MES enables real-time visibility into resource availability, allowing manufacturers to allocate resources efficiently and effectively. By optimizing production schedules, manufacturers can improve on-time delivery performance and optimize resource utilization, resulting in cost savings and increased customer satisfaction.
What are the challenges of using a MES?
One of the primary challenges in MES implementation is the integration with existing plant systems and technologies across multi-site operations. Due to a legacy of mergers and acquisitions, manufacturers often have a complex network of systems, such as different supervisory control and data acquisition (SCADA) systems and various automation technologies. An effective multi-site MES approach should agnostically connect and seamlessly integrate with these systems to enable consistent KPIs, operational reporting, and data exchange.
Integration and MES standardization requires careful planning, collaboration between different teams, and a center of excellence approach to the standardization of interfaces and protocols. By addressing integration challenges, manufacturers can shorten the time to benefit, minimize the cost of ownership, and maximize the return from their existing plant investments.
Here are some tips to set your MES up for success:
- Firstly, it is crucial to define clear objectives and align them with the overall business strategy. This ensures that the MES implementation addresses business priorities, improves operational efficiency, and supports long-term growth.
- Secondly, involving key stakeholders from different departments to create a center of excellence—including production, quality assurance, maintenance, and IT—is essential. A center-of-excellence approach to large-scale, complex MES programs accelerate adoption across the enterprise and ensures that the MES solution caters to the unique needs of the business and facilitates smooth plant operations.
- Comprehensive training and change management programs should be implemented to ensure user adoption and system acceptance. Employees need to understand the benefits of the MES and how it can improve their daily operations. Training sessions, workshops, and continuous support during the transition period play a vital role in maximizing the potential of the MES.
What is the future of manufacturing execution systems?
MES is poised to play a central role in Industry 4.0, characterized by the fusion of physical and digital technologies. With the advent of smart factories and cyber-physical systems, MES will be integral to the transformation of manufacturing plants into smart factories, enabling manufacturers to reap the benefits of this transformation. From predictive analytics to artificial intelligence, MES and operational data management will facilitate higher levels of productivity and agility as manufacturers look to empower their people, connect and compare their plants to optimize operations, and enable a connected ecosystem.