Hennig-Olsen
“The most important improvement is that we now have one single system for our entire operation that allows us to be more flexible when it comes to personnel and suppliers, by providing a standardized system and a higher level of automation.”
– Marianne Stordal; Director of Production, Hennig-Olsen
Goals
- To establish a standardized software system with in-house control to accurately track production processes
- To effectively manage quality operations ensuring product safety and compliance
- To strengthen inventory control, traceability of material usage
Challenges
- The previous system did not allow for immediate access to reporting and plant data metrics
- Quality measurement data such as product temperature and maturity tracking was unreliable
- Management was unable to effectively manage the production of its various food products throughout its manufacturing facilities
Results
- The company can successfully track processes from warehouse, to the production lines enabling it to maintain is 48% marketshare
- Operations are simplified and the company is able to measure materials in real time anywhere, as well as know the specific batch, date and amount of ingredients used
AVEVA Software Ensures Hennig-Olsen Churns out Only the Tastiest Ice Cream Treats
HANNEVIKA, Norway – For more than 90 years, Hennig-Olsen has been bringing tasty ice cream treats to the Nordic region and maintains 48 percent of the region’s market share. Producing approximately 30 million liters of ice cream and frozen desserts each year is not an easy feat, and requires meticulous recipe management and quality-control of ingredients at its factory in Hannevika, Norway.
In recent years, the production management team realized that their in-house-developed automation system couldn’t keep pace with the factory’s growing manufacturing requirements.
“The information being generated from the existing system, such as production reports, wasn’t accurate, and accessibility to critical data was limited. Our goal was to find a standard solution, since our existing in-house solution was too expensive to maintain and was failing to provide the critical data such as temperature supervision and maturity tracking we required as a premium ice cream products manufacturer.”
– Gudvin Baldersheim; IT Manager, Hennig-Olsen
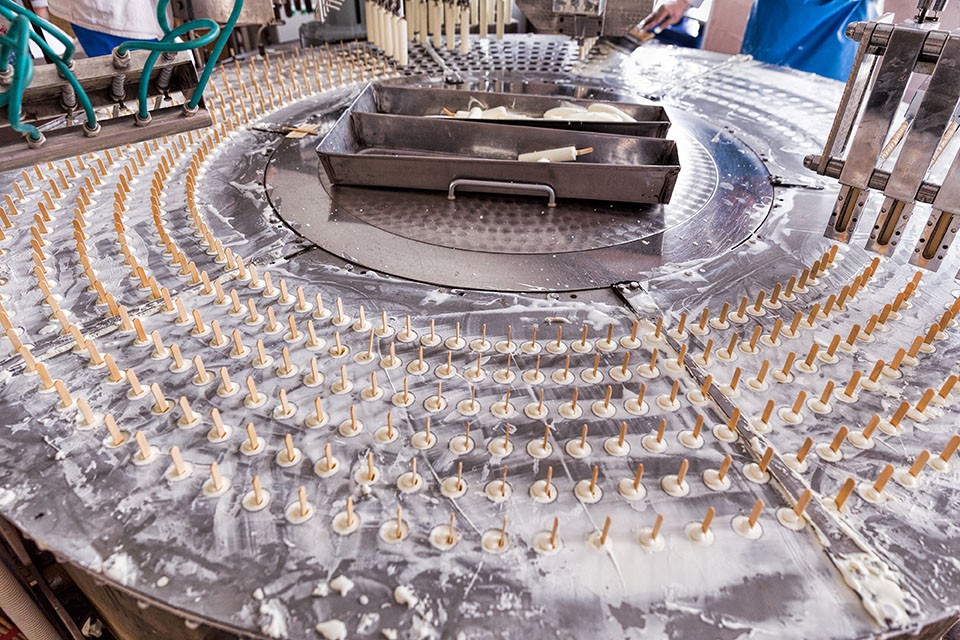
AVEVA Software Provides Flexible MES Solution
“The Wonderware MES solution was chosen based not only for financial reasons, but also security reasons as well. Using real-time production information, decision makers and operators can effectively manage the order flow and production execution, tracking the transformation of products from raw materials through finished goods, and gathering real-time information on yields, quality, resource and asset management.”
– Marianne Stordal; Director of Production, Hennig-Olsen
The Wonderware MES solution is a comprehensive Manufacturing Enterprise System (MES) solution which tracks processes from warehouse, to the production lines.
In addition, the flexibility of Wonderware MES enables Hennig-Olsen to use the solution in any scale and scope to satisfy different approaches to MES, either growing from equipment-focused MES for work order execution, traceability, overall equipment effectiveness, or from a real-time enterprise strategy, integrating more and more of the production process into the business process information flow.
“The Wonderware MES solution is based on a very flexible and modular database with an extensive set of functions available. I think the flexibility in the database is the most important asset of the architecture of the Wonderware software to meet the needs of Hennig-Olsen.”
– Ole Petter Drangshold; Osterhus, the Wonderware system integrator for the project
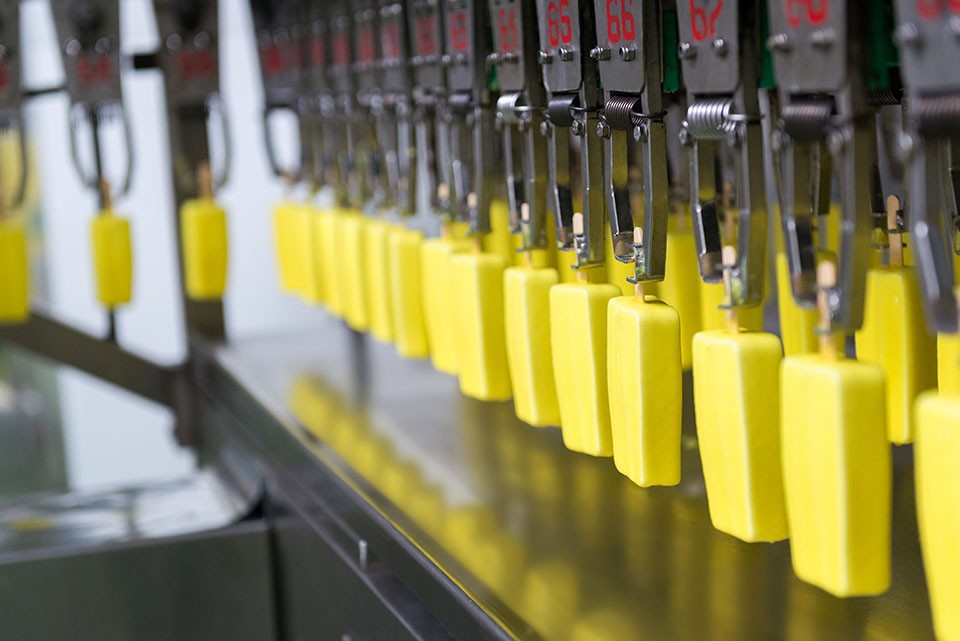
Wonderware MES Enables Real-Time Visibility and Monitoring
Wonderware MES also enables the manufacturing team at Hennig-Olsen to improve asset utilization with real-time equipment monitoring. This provides key performance indicators (KPIs) such as overall equipment effectiveness (OEE) for tracking, and analyzing the successful use of assets in the production process.
“We can now access information at any time, which makes it much easier for my team to implement predictive maintenance procedures in a much timelier fashion.”
– Kai Tobiassen; IT Manager of Production, Hennig-Olsen
By integrating with plant equipment and data sources, Wonderware MES provides real-time condition and status information to Hennig-Olsen’s decision-making process. Operators can effectively manage the use of raw materials and manufacturing processes to gain the highest possible efficiencies, while meeting regulatory and operations goals for profit, quality, uptime and yields.
In addition, critical equipment downtime and efficiency information is communicated in real-time to operators and decision-makers who can take immediate action to improve plant performance and productivity.
With the capability of the MES to track raw materials across the entire production process, the system provides huge cost savings to Hennig-Olsen.
“In terms of tracking, we have simplified our operations and we can now measure materials in real-time anywhere, as well as know the specific batch, date and amount of ingredients that we use.”
– Kai Tobiassen; IT Manager of Production, Hennig-Olsen
The Best MES Solution for the Region’s Best Ice Cream Maker
Hennig-Olsen is now able to provide higher product consistency, production and process efficiency as well as repeatability across various production lines with the use of Wonderware MES.
Wonderware MES also offers real-time visibility into the full range of production processes, from production planning and setup to actual execution of operational activities. Production managers and planners can build and view material specifications and grades, bills of materials, manufacturing procedures or steps, as well as define production routing.
During production, Hennig-Olsen can now track real-time and historical material and labor consumption, lots, WIP inventory, waste, yield and finished good totals, along with other important production events. By providing visibility to all of Hennig-Olsen’s production information, Wonderware MES enables the production teams to focus on operating its manufacturing facility in the most efficient and productive manner possible.
“The Wonderware solution turned out to be a great decision with rich functionality that covers all of our needs. We now have better control of production process to better track use of raw materials and finished products, which is a huge step forward for us. This is particularly important on the financial side to reduce loss in production and control costs, and we’ve accomplished this goal. Wonderware MES has turned out to be the best solution for the best ice cream manufacturer.”
– Gudvin Baldersheim; IT Manager, Hennig-Olsen
Related Success Stories
Stay in the know: Keep up to date on the latest happenings around the industry.